To consider an application for financing, fill out the form and send it to us by e-mail along with the project brief, or contact our experts
SI offers a full range of financial and engineering solutions for the modernization of cement plants around the world.
We and our partners implement successful projects in Europe, North Africa, South America and the Middle East, contributing to the achievement of business goals.
One of the challenges for the cement industry in developing countries is the wet manufacturing process.
Outdated technologies consume a huge amount of energy, which negatively affects the competitiveness of products.
In addition to switching to a dry process in cement production, our engineering company implements other projects leading to increase the efficiency of existing cement plants.
This includes the modernization of cement kilns, the introduction of vertical cement mills, as well as the design and installation of renewable energy equipment.
The increase in production and efficiency is reflected in the achievement of the impressive financial results that our customers demonstrate shortly after modernization.
Improving the energy efficiency of cement production
The cement industry has a very high energy consumption, which depends on the process and equipment used. The main types of energy for cement production are heat and electricity.In the context of rising prices for natural resources, the energy efficiency of cement plants, both in terms of heat and electricity consumption, has remained one of the top priorities for many decades.
Engineers offer engineering services in the field of optimizing cement production and increasing its energy efficiency. We carry out a comprehensive modernization of cement plants anywhere in the world.
Designing new clinker production lines, minimizing losses of electric and thermal energy at all stages of the technological process, using renewable energy sources and much more. We will develop an individual solution for your business.
Energy consumption in cement production
The theoretical amount of thermal energy for the production of cement clinker is determined by the energy necessary for burning clinker (about 1700-1800 MJ / t) and the heat necessary for drying and preheating of raw materials.Consumption mainly depends on its initial moisture content.
Practice shows that the energy consumption of dry process cement plants with multi-stage cyclone preheaters and furnaces varies widely. These differences are due to shutdowns and even restarts of equipment, as well as to significant differences in the quality of raw materials.
The main consumers of electrical energy are cement mills, as well as exhaust fans. This equipment accounts for more than 80% of total energy consumption. On average, energy costs (including fuel and electricity) account for approximately 40% of total cement production costs.
Electrical energy accounts for up to 20% of the energy consumption of a cement plant. Electricity consumption varies from 90 to 150 kWh / t of cement, while a wet process is much more energy intensive than a semi-wet or dry process.
Electricity consumption also depends on the nature of the product and the degree of grinding. In many cases, energy use can be minimized by replacing obsolete clinker production lines.
Production waste is often used to generate energy and reduce dependence on traditional fuels. This trend has been growing steadily over the past few decades.
Being a highly developed and established industry, the cement industry does not expect radical changes that could significantly reduce energy consumption. Over the past 25 years, the efficiency of the global cement industry has improved mainly due to the dry process.
If you are thinking about financing, modernization and construction of new facilities, SI is ready to offer the best solutions for your business.
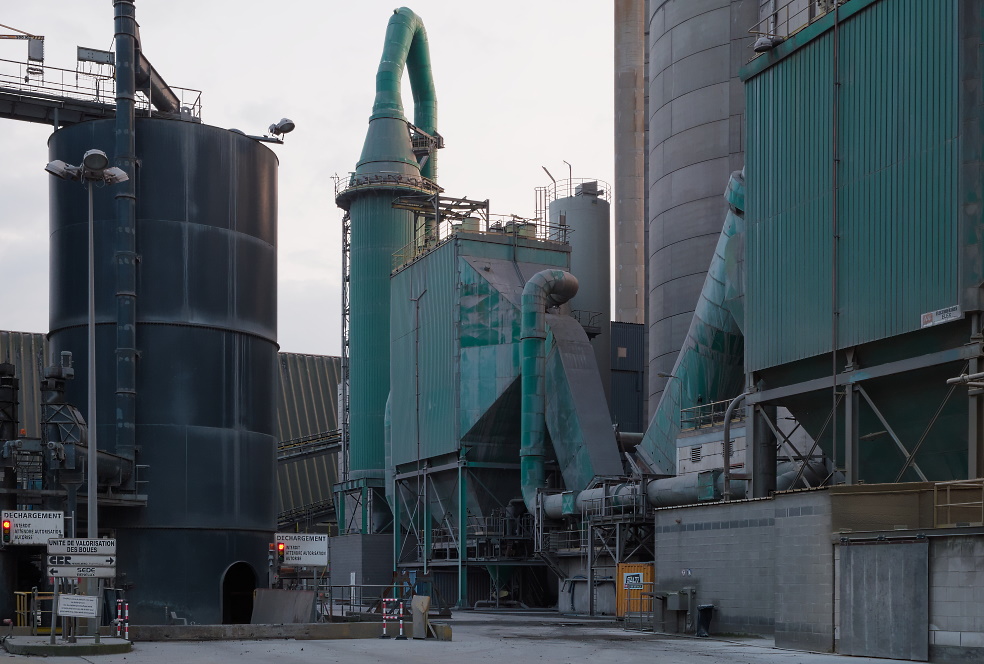
Preparation of raw materials and fuels
One of the main opportunities for energy saving is the installation of highly efficient systems for transporting raw materials and fuel.Pneumatic or mechanical conveyors are usually used for this purpose, but mechanical equipment consumes less power.
According to studies, the potential energy savings resulting from the transition to mechanical conveyor systems are about 1.8-2.0 kWh / t.
Replacing high-power bucket elevators with pneumatic conveyors for moving materials to heaters and grinding bins reduce energy consumption by 60-65%. To determine the investment costs and the payback period, our specialists need to assess the situation at a particular plant.
Production of a high-quality product and maintaining optimal combustion conditions will require complete homogenization of the material. The modernization of grinding equipment reduce heat consumption by 20 MJ / t, and the consumption of electric energy by 0.7 kWh / t.
Old cement plants use compressed air to mix the raw mix. Energy consumption in this case reaches 1.5 kWh / t. In modern plants, more efficient gravitational homogenizers (0.1-0.5 kWh / t) are used for this purpose.
Traditional ball mills, which are used to grind certain types of raw materials (limestone), can be replaced by roller mills. Highly efficient grinding equipment saves energy without compromising product quality.
It is believed that the installation of vertical or horizontal roller mills can lead to energy savings of up to 6-7 kWh / t. An additional advantage of this modernization is that vertical roller mills are able to combine the drying of raw materials and the grinding process.
The raw materials for the production of cement have different grindability. Harder materials require more energy to achieve the desired particle size. Different materials must be ground with appropriate equipment, focusing on energy savings.
As in previous cases, a strictly individual approach to improving the energy efficiency of cement production is required.
A relatively recent development is the use of classifiers. Highly efficient classifiers separate small particles and return large particles back to the mill.
Fuel preparation for a cement plant is most often performed at the production site. This step may include crushing, grinding and drying the coal.
The use of roller mills allows you to grind coal without preliminary crushing, as well as effectively process coal with a high moisture content. Vertical roller mills designed for grinding coal are widely used in the cement industry. Their energy consumption of is about 16-18 kW / t of coal.
Roller presses similar to those used to grind cement and raw materials are generally more efficient than conventional mills. They are used to grind both raw materials and coal, although coal grinding equipment should also have special explosion protection.
Clinker production modernization
Heat loss by the kiln can occur if the process conditions are not appropriate or the it is not properly controlled.Automated control systems can optimize these conditions depending on the fuel type. Automation helps to improve the quality and grindability of the product.
Clinker production modernization may include the installation of analyzers that allow operators to determine the chemical composition of raw materials, making timely changes to the process.
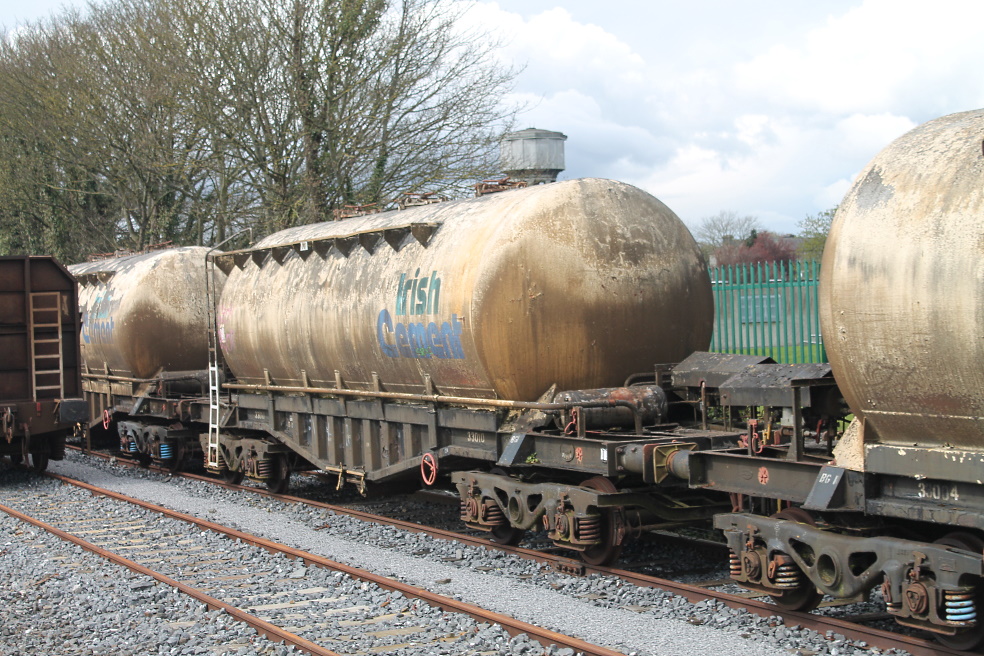
A homogeneous mixture ensures stable operation of the kiln, which also leads to significant fuel economy. Energy savings resulting from the installation of modern control systems can range from 3 to 10%. The payback period can reach only 3 months.
Outdated clinker burning systems have low efficiency due to problems such as poorly controlled combustion, incomplete combustion with a high formation of carbon monoxide.
Advanced systems are characterized by a more suitable flame shape, complete combustion of fuel and less use of air.
Modern flame control technologies can save up to 10% of fuel, depending on the type of cement kiln. Today, it is common practice to recycle gases from the end back to the combustion area, which improves flame stability and protects the surface from burning particles.
Installing fan control system can result in lower energy consumption and lower maintenance costs. The energy savings resulting from the implementation of this measure vary, as the configuration of the fan system can vary significantly. Practical experience shows that installing frequency controllers on fans can reduce energy consumption by 5 kWh / t.
The exhaust gases from the kiln and clinker cooler are a source of energy that can be used to dry raw materials or to generate electricity. Heat recovery can provide significant savings of up to 30%.
The approach to modernization of heating systems depends on the characteristics of raw materials and the production process. When the moisture content of the feed exceeds 8%, the heat demand is high. Under these conditions, multi-stage heating systems demonstrate the greatest efficiency.
Another measure is the installation of a precalciner and, where possible, an additional heater.
The precalcinator increases plant productivity, helping to reduce fuel consumption and nitrogen oxide emissions.
Equipment for grinding cement
Finished product grinding systems are developed using that approach.These engineering solutions must control the operation of the mill and classifier, ensuring a stable output of high-quality cement.
One of the directions of modernization of grinding equipment is the measurement of particle size in real time. The control system ensures the production of cement, which exactly meets the specified requirements and standards.
This solution can reduce electricity consumption at the stage of cement grinding by 15-20%. With this level of energy savings, the estimated payback period is about 2 years.
The energy efficiency of ball mills for cement production is relatively low.
This equipment usually consumes up to 30-40 kWh / t depending on the particle size of the finished product. But there are several alternatives that can reduce energy consumption to 20-30 kWh / t clinker.
Among them are roller mills and roller presses, which can be used separately or in combination with ball mills for pre-grinding.
These and other measures play an important role in the modernization of cement plants. In each case, the choice of technology should be individual, taking into account the type of the process, equipment and raw materials.
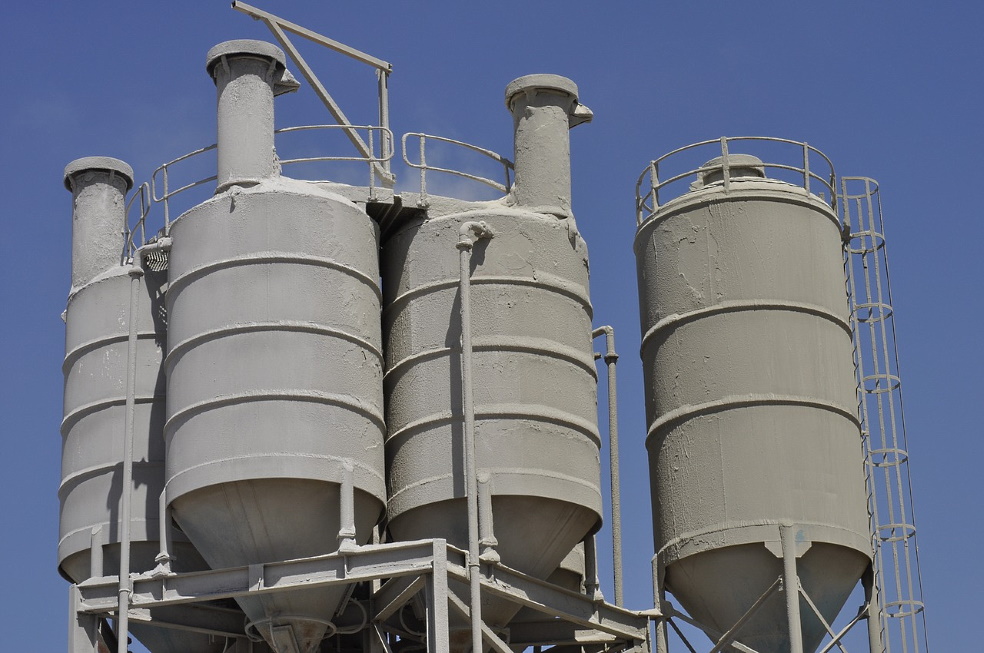
Cement plant modernization
SI with partners offers solutions in the field of industrial automation and modernization of industrial facilities.We offer financing, construction and modernization of existing cement plants around the world, including the construction of a dry cement production line and the introduction of innovative energy-efficient technical solutions.
Engineers strictly comply with all the standards and parameters of the project, providing comprehensive coverage of the needs of our customers. We are known for the uncompromising quality of services and the reliability of the proposed technical solutions.
Cement plant modernization services cover:
• cement mills;
• rotary kilns for the production of cement clinker;
• clinker coolers;
• dosing equipment;
• loading systems for raw materials and finished products;
• packaging lines for finished products;
• production automation systems and much more.
A high level of professional competence contributes to the excellent results of technical and business cooperation.
Improving environmental performance of cement plant
Cement production, including the processing of raw materials and additives, combustion of fuel and waste, is associated with significant emissions of pollutants into the atmosphere.Cement plant modernization usually require modifications to production processes to minimize harmful emissions.
Non-compliance with national and international standards can result in large financial and reputational losses for manufacturers.
The list of major air pollutants includes:
• metals and their compounds;
• sulfur dioxide and other sulfur compounds;
• nitrogen oxides and other nitrogen compounds;
• volatile organic compounds (VOCs);
• polychlorinated dibenzo-p-dioxins and dibenzofurans (PCDD and PCDF);
• hydrogen fluoride (HF), hydrogen chloride (HCl) and carbon monoxide.
Cement production is also associated with the release of significant quantities of carbon dioxide.
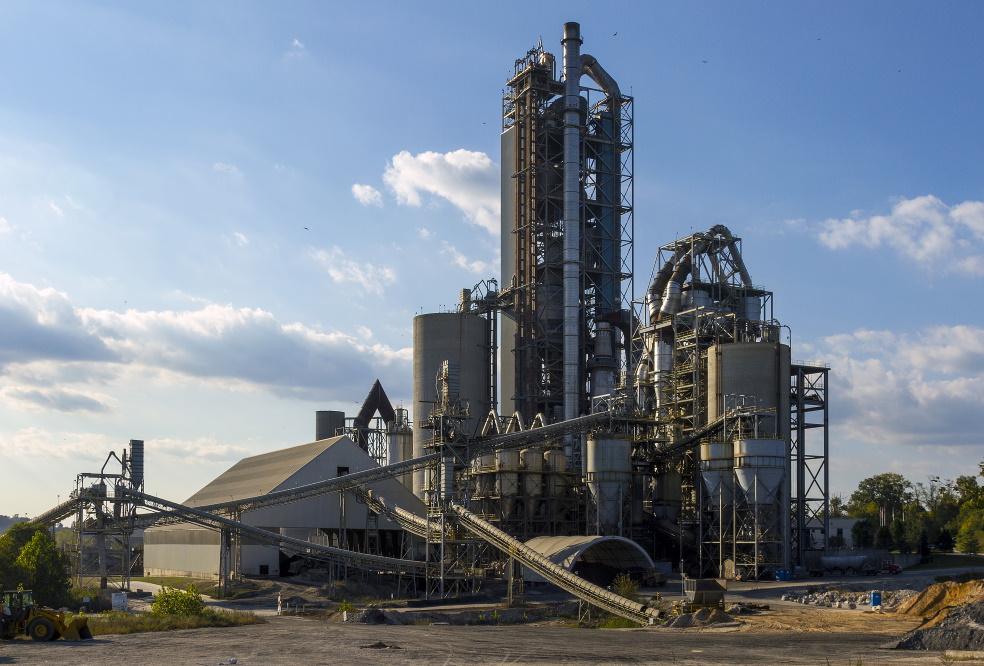
The main pollutants in the cement industry are emitted by the kiln system as a result of physicochemical reactions involving raw materials and burning fuel.
Gases from a cement kiln contain mainly nitrogen from the air, as well as carbon dioxide generated during calcination of calcium carbonate and combustion, as well as water vapor.
Many substances resulting from the combustion of fuel or the conversion of a raw material mixture into clinker remain in the gas phase only until they are adsorbed or condensed on moving particles of the raw material. This process depends on the location of solid particles in the kiln.
The absorption capacity of a material can vary significantly depending on its physico-chemical properties. For example, calcined material has a high calcium oxide content and, therefore, it can easily adsorb acidic compounds such as HCl, HF or sulfur dioxide well.
The emission characteristics of kilns largely depend on the composition of the raw materials and fuel used, the age of the plant, and the design features of the equipment.
Modernization of cement kilns is an important step to minimize emissions.
Sources of emissions from cement production
The main sources of dust emissions are raw material preparation processes, including grinding and drying (mills and dryers), clinker burning (kilns and clinker coolers), fuel preparation systems and coal grinding mills.Diffuse dust emissions can occur during storage and transportation of raw materials or solid fuels. Sources of such pollution can be open warehouses, conveyor belts and driveways.
Clinker burning is a high-temperature process leading to the formation of nitrogen oxides.
These potentially harmful substances are formed during combustion.
Sulfur dioxide emissions are dependent on the total amount of sulfur compounds used. They are mainly determined by the content of volatile sulfur in the material and fuel.
Organic impurities from natural raw materials during the clinker burning process cause significant emissions of carbon monoxide and organic carbon substances.
Emissions of polychlorinated dibenzodioxin and dibenzofuran (PCDD / F) depend on the kiln design, combustion conditions, quality of raw materials and equipment for emission control.
PCDD / Fs can also form during or after preheating if the feed contains a sufficient amount of chlorine and hydrocarbon precursors.
Emissions of hydrogen chloride and hydrogen fluoride are usually small. They are the result of certain substances entering the kiln system.
Ammonia emissions occur at the initial stages of the raw material production process, and the ammonia content in flue gases reaches 200 mg / m3. Additional emissions of unreacted ammonia are generated using certain technologies, such as selective non-catalytic reduction (SNCR).
Other organic pollutants released during cement production are chlorobenzenes and polychlorinated biphenyls. Measurement of these substances is recommended under special operating conditions.
Cement plants are major sources of carbon dioxide emissions. According to studies, the cement industry emits approximately 2.5% of global CO2 emissions from industrial and energy sources.
Carbon dioxide is released during the production of clinker. This is a by-product of calcination, which forms in the upper, colder part of the kiln.
All of the substances listed above contribute significantly to global air pollution.
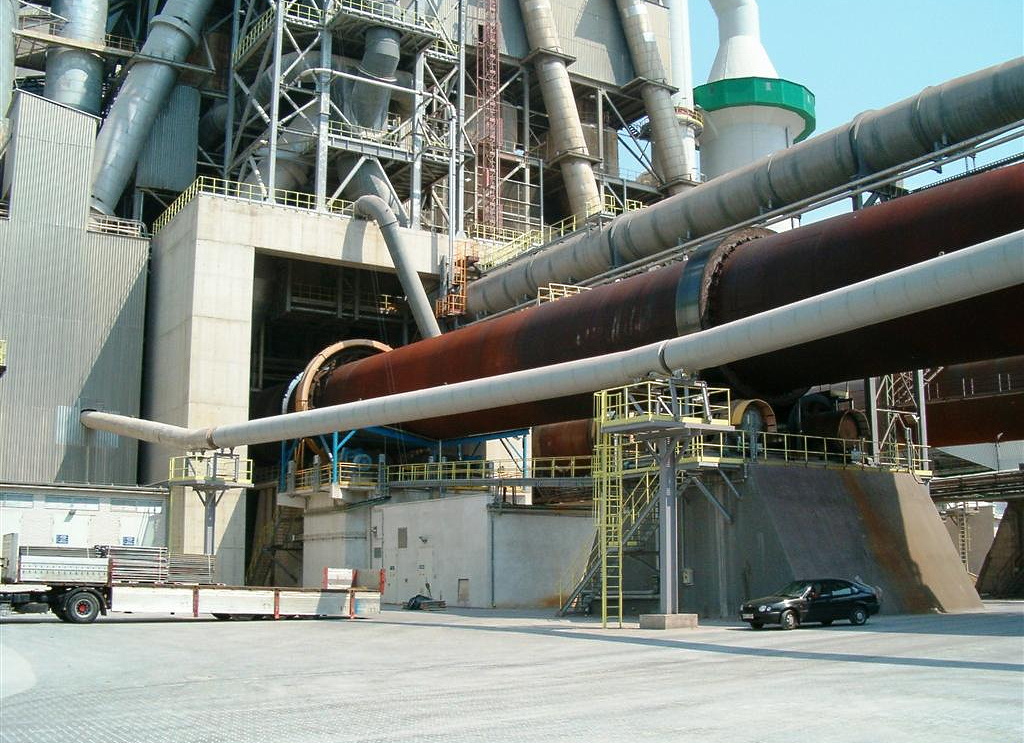
As a result of stricter environmental requirements, many companies are increasingly focusing on emissions, but the business is not ready to invest heavily in the ecological modernization. We can offer a comprehensive package of measures tailored to your budget.
Engineers will analyze your production process and equipment, developing effective proposals to improve the environmental performance of the cement plant.
Dust control measures
Most of the emissions (PM 10, PM 2.5) can be reduced by reducing dust and introducing highly efficient dust extraction systems.In the past, various dust collectors have been used for this purpose.
Today, bag filters, electrostatic precipitators, or combinations of these two types (hybrid filters) are the most common.
Collected dust can be returned back to production processes, if technically possible. It can be returned directly to the oven or mixed with finished products. Alternative methods are used to recover material that is not suitable for reuse.
Nitrogen oxide emissions
During the ecological modernization of cement plants, much attention is paid to minimizing emissions of nitrogen oxides and other nitrogen-containing compounds, which are formed mainly during the combustion process.Combinations of primary and / or secondary methods integrated into the process may be used to control nitrogen oxide emissions.
These methods include:
• decrease in flame temperature;
• use of more efficient burners;
• improving the combustibility of the material;
• gradual burning with conventional fuel or waste;
• use of optimized fuel mixture.
Additional techniques such as selective non-catalytic or catalytic reduction can be used.
Sulfur dioxide emissions
Measures to reduce sulfur dioxide emissions include improving clinker burning efficiency, uniform distribution of raw materials and careful control of the quality of raw materials and fuel.In this regard, the concentration of oxygen is extremely important.
An increase in oxygen concentration helps to reduce the level of sulfur dioxide, but increases the content of nitrogen oxides.
However, to achieve a given product quality, clinker burning requires an excess of oxygen.
Emissions of CO and volatile organic compounds
Raw material selection is critical in terms of reducing CO emissions.Where possible, raw materials with a low organic content are preferred. Other options include optimization of the clinker burning process, modernization of the burners, as well as regulation of the temperature and time of burning.
Under normal conditions, emissions of volatile organic compounds (VOCs) are generally small.
Their number can increase with a high content of organic volatile substances in the raw material.
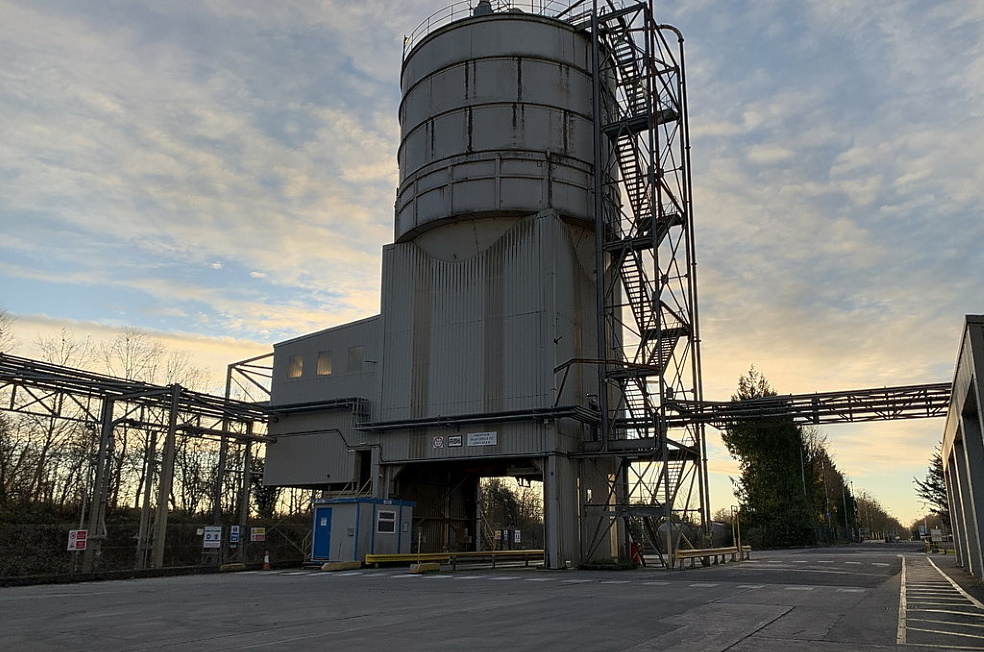
A certain amount of VOC can be adsorbed using activated carbon.
Our company uses highly efficient European technologies to reduce emissions of volatile organic substances and carbon monoxide in cement plants.
PCDD / F emissions
Cement kilns typically emit very low amounts of PCDD / F.To minimize their concentration, it is necessary to ensure the stability of the burning process.
This is achieved in the following ways:
• use of modern fuel systems;
• introduction of computerized control systems;
• minimization of fuel consumption by pre-heating;
• use of raw materials and fuels with a low content of organic substances.
Experts recommend limiting the use of waste if it contains organic chlorinated substances. It is also not recommended to use spent fuel when starting and stopping equipment.
Excessive PCDD / F concentrations can also be reduced with activated carbon.
Metal emissions
The use of materials with a high content of volatile metals such as mercury and thallium should be monitored with particular care.These impurities can lead to increased toxic emissions and their accumulation in clinker and dust.
Since the metals emitted are largely associated with dust, metal emission control strategies overlap with dust control measures. Effective dust removal also reduces metal emissions.
One way to minimize mercury emissions from cement plants is to lower the temperature of the gases. Due to this, non-volatile elements remain in the cement clinker.
Activated carbon can also be used to trap some metals.
New technology contributes to a significant improvement in the environmental performance of cement plants.
We can offer the most effective and safe solutions for your business.
If you want to know more about financing and modernization of cement plants, contact us any time.