To consider an application for financing, fill out the form and send it to us by e-mail along with the project brief, or contact our experts
The design of mining and processing plants is a complex task, which is solved by multidisciplinary teams of engineers, geologists, architects, economists, marketers and other specialists.
Compounds of gold, silver, copper, zinc, iron, nickel, chromium, aluminum, titanium, lead - the range of valuable materials produced by mining enterprises includes hundreds of items.
Each project of a mining and processing plant is another challenge for engineering companies, requiring unique technical and logistic solutions.
Over the past decades, the cost of minerals has been growing. Compared to the 1960s, the world production of rare metals has increased more than 10 times. The global economy's demand for metals, including non-ferrous metals for electronics and high-tech industries, is growing.
This trend forces companies to increase production and seek innovative solutions to succeed in the struggle for global markets.
List of the largest metallurgical and mining companies in the world in 2019:
# | Company name | Country | Turnover, USD bln |
1 | Glencore | Switzerland | 215 |
2 | China Minmetals Corporation | People's Republic of China | 85 |
3 | ArcelorMittal | Luxembourg | 70 |
4 | POSCO | South Korea | 55 |
5 | BHP Billiton | Australia, UK | 44 |
6 | Rio Tinto | Australia, UK | 43 |
7 | Vale SA | Brazil | 37 |
Extraction and processing of minerals is a driver of the development of the renewable energy sector.
According to the World Bank, mining companies will have to ramp up production of lithium, cobalt and graphite by almost 5 times by 2050 to meet the growing needs of the renewable energy sector, including the development of energy storage technologies.
Given the global environmental degradation and depletion of mineral resources, the SI and our partners are striving to make ore processing more efficient and environmentally friendly. We solve the most ambitious tasks using rich experience and advanced European technologies.
We work with leading mining equipment manufacturers to bring your investment project to a high technical level.
Our long-term partnerships with reputable scientific institutions, construction teams and engineering companies in United Kingdom, USA, China and other countries will be the key to the success of your project.
Most of our projects are carried out under an EPC contract, which means additional benefits for our customers.
Are you looking for a reliable partner for financing and construction of a mining and processing plant?
Contact our representatives to learn more about our services.
Mining and processing plant design
The design of mining enterprises begins with numerous studies, including the determination of the mineralogical composition of the ore, the possibilities of its industrial processing, the analysis of market conditions and customer requirements, possible restrictions on commercial activities, and so on.A clear understanding of the possibilities and limitations of a particular project is a prerequisite for a safe investment.
There are general requirements for all projects of plants that are engaged in the processing of minerals:
• Providing highly efficient ore processing with minimal waste.
• Rational layout for the most efficient use of land and natural resources.
• Ensuring high safety and reliability of technological processes without risk to the environment and people.
• Application of advanced technologies to achieve high productivity and economic results.
• Creation of an optimal scheme for supplying the plant with water, electricity and other resources.
When preparing technical documentation for the construction of a mining and processing plant, an engineering company has to carry out large-scale research and design work.
As a result, the general contractor can offer the best way to implement the project in one form or another, taking into account a number of economic, technological, geophysical, hydrological and other parameters.
General information about the project of the mining and processing plant contains the following:
• Initial data for the development of project documentation.
• Description of the technological process, parameters and requirements for product quality.
• Description of the plant's raw materials base, the need for additional fuel and resources.
• General characteristics of the future facility with its equipment and staff.
The type of plant, the features of the ore processed, the availability of resources, the project budget and other factors have a significant impact on the final appearance of the plant, which will be presented in the technical documentation.
Each customer needs an individual approach and unique engineering and technical solutions, which is confirmed by the practice of building mining and processing plants around the world.
The engineering design of mining and processing plants includes:
• Investigation of the land plot (topographic, geological, meteorological, geological) with substantiation of specific solutions for its comprehensive preparation, strengthening and protection from possible natural disasters.
• Zoning of the construction site indicating the location of the main and auxiliary structures.
• Selection of the optimal scheme of access roads, transport hubs, pipelines and power lines.
• Development of technical solutions aimed at ensuring the stability and safety of engineering structures.
• Substantiation of architectural solutions, including general layout, detailed plans and purpose of structures.
• Development of a technological chain for ore processing and beneficiation, including the development of chains of ore supply, storage and shipment of finished products, handling of intermediate products, etc.
• Development of the plant's power supply system, indicating electrical substations, power lines, backup power supplies, lighting systems, communications, lightning protection devices, grounding and much more.
• Information on the water consumption of the enterprise with a detailed plan for water supply and sewerage, including the development of sources of technical and drinking water, fire extinguishing systems, storm sewer systems, and so on.
• Engineering solutions in the field of HVAC and industrial heating networks, including the development of the most efficient sources of heat supply for the mining and processing plant and air conditioning systems.
• Measures to protect the environment and public health, including engineering design of equipment for air purification, individual solutions for waste disposal and wastewater treatment, measures for the rational use of natural resources.
The above list demonstrates only a fraction of the challenges that the engineering team faces when designing mining enterprises. A professional approach to these projects allows our customers to save valuable mineral resources and water, minimize greenhouse gas emissions and achieve sustainable business development.
Technological processes of ore dressing at mining and processing plants
Natural raw materials of mineral origin usually do not have properties that allow direct commercial use.For example, most non-ferrous metals are currently obtained from ores with 1% content of these metals or even less. Such ores in their raw form cannot be used in industry.
Almost all minerals, as well as metallurgical waste, must first undergo multi-stage processing.
In the engineering design of a mining and processing plant, it is important to use the most suitable technological processes that allow obtaining the maximum amount of valuable materials with minimum investment costs.
To achieve this goal, the physical properties of the ore, its chemical composition, mining conditions and many other factors should be taken into account.
The main technological stages of ore dressing include:
• Reduction of the size of ore particles (communition), which is carried out using crushing machines (crushing) and mills (grinding).
• Separation of the resulting particles of different sizes (sizing), which requires the use of different screens and classifiers.
• Increasing the percentage of valuable material in the product (concentration), which is carried out using various technological methods depending on the properties of the material (flotation, magnetic separation, etc.)
At the final stage of ore processing, it is necessary to bring the product into an appropriate condition, allowing it to be transported and delivered to the end consumer. This stage usually includes thickening, dewatering and pressing of ore beneficiation products. After that, the recovered process water is reused in production, and the finished product is sent to the warehouse.
The engineering design of equipment for sludge treatment and process water purification plays an important role in increasing the efficiency of the production process.
Engineers use advanced technologies that have already proven their reliability in mining and processing plants around the world. The main goal in each project is to ensure high productivity, reliability, environmental safety of all technological processes in accordance with the customer's requirements.
Equipment for crushing ore (crushing)
Crushing is one of the main processes in the mining and processing industry, as well as in the production of aggregates for construction.The selection of a crusher for processing metallic and non-metallic ores depends on the specific application, Equipment requirements are based on characteristics such as desired outlet particle size, ore grain size, material structure (crystalline, amorphous, porous, fibrous), crush and impact resistance, risk of spontaneous ignition due to the heating of materials during grinding, etc.
Crushing machines are characterized by significant energy consumption, therefore crushing is carried out only to the extent necessary to prepare the material for further processing. Excessive crushing results in higher production costs with no clear advantage in terms of quality and productivity.
Crushing equipment is classified according to the degree of crushing, principle and mobility:
• The degree of crushing: crushers of coarse, medium and fine crushing.
• The principle of operation: jaw, conical, roller, rotary, and centrifugal crushers.
• The mobility: stationary, mobile and semi-mobile crushers are distinguished.
The main trend in the engineering design of mining and processing plants is the use of jaw crushers for the coarse crushing stage, as well as cone and impact crushers for medium and fine crushing.
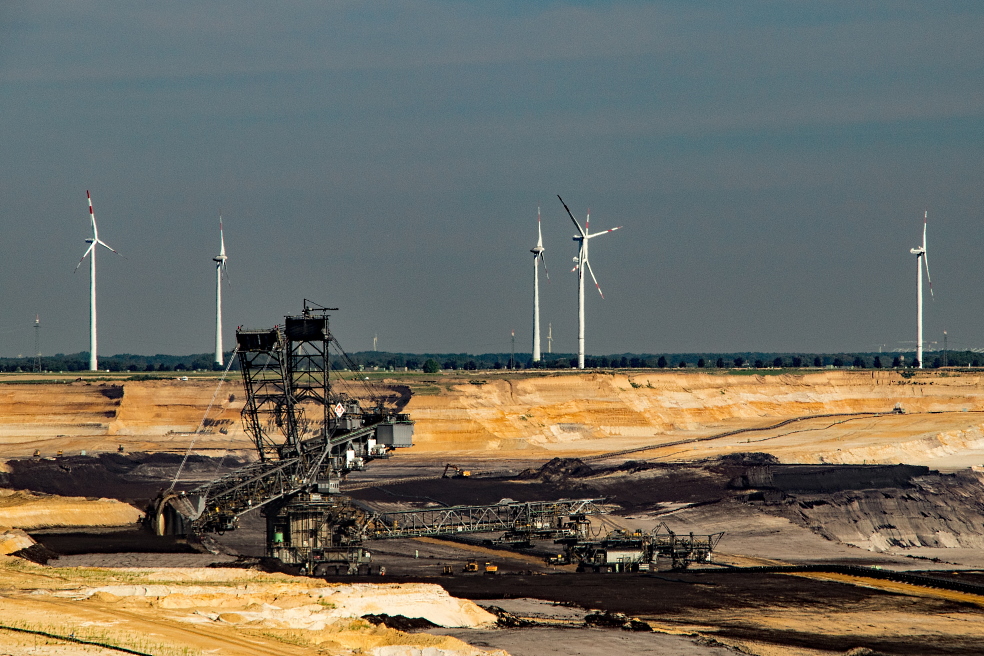
Jaw crushers
Jaw crushers are used for primary or secondary crushing of granite, basalt, diabase, gabbro, slag, carbide and many other materials. Material falls between two machine jaws at a specific angle.One part is mobile and periodically approaches the other fixed jaw. Most often, this contact angle is 15-20 degrees. To protect against wear, the jaws are equipped with replaceable manganese-alloyed hard steel crushing plates. The plates have longitudinal ribs that increase the bending effect during crushing.
Jaw crushers are the preferred equipment for primary ore crushing. In practice, jaw crushers with a simple or complex jaw trajectory are usually used.
The latter are mainly used for finer crushing of material.
In jaw crushers with complex jaw movement, the movable part is connected to the crusher frame and is driven by an eccentric shaft that rotates around an axis. Points at the top and bottom describe closed curves that are close to a circle, and intermediate points describe elongated closed curves. The complex movement pattern crushes the material much more evenly than with simple jaw movement crushers.
Cone crushers
Cone crushers are widely used for coarse crushing of ore between movable cones. They are installed mainly in quarries, mines, cement plants. This principle of operation provides a fairly high performance.The crusher's inner cone moves eccentrically in a stationary outer cone. It is driven by an eccentric sleeve that rotates in a bevel gear. The crushing process resembles crushing in jaw crushers, with the difference that it is continuous, and the angle of capture of particles here is determined constructively and does not depend on the size of falling particles.
The crushing surfaces are made of solid manganese steel and have longitudinal ribs to increase the bending effect.
Roll crushers
Roll crushers are used for medium to fine crushing of softer materials such as clay, feldspar, limestone, marl, as well as coal, oil sands and overburden.In these machines, material is continuously crushed between two cylindrical rolls that rotate in opposite directions at the same or different speeds. The final particle size of the crushed material is determined by the distance between the two rollers.
In the engineering design of mining and processing plants, the three most common types of roller crushers are used. These can be machines with one or two movable rolls, as well as crushers with fixed rolls.
In devices of the first type, the bearings of one roll are fixed, and the bearings of the other roll are pressed by springs against fixed supports.
Plates are installed between the bearing and the support, adjusting the distance between the rolls. The force of the springs is adjusted so that the bearings are always pressed against the supports under normal operating conditions. Accidentally falling between the rollers, a solid object immediately displaces the movable backup roller, overcoming the forces of the springs and passing the material between the rollers. When only one of the rolls moves, the machine and its foundation are subject to strong horizontal shocks.
As for the second type of crusher, such problems do not arise, since both rolls can be displaced when a solid object hits. This type of crusher is technically complex and less common. In machines of the third type, the rolls are fixed immovably, and therefore random solid objects cannot pass through them.
An overload clutch shuts off the machine in case of overload.
Impact crushers
Impact crushers installed at mining and processing plants are used for coarse, medium and fine crushing of brittle materials with relatively low hardness and abrasiveness (limestone) and a maximum permissible moisture content of up to 15%.The material is crushed mainly by the impact of the rapidly rotating hammers.
Impact crushers are usually divided into two broad groups, depending on the way the hammers are attached to the rotor of the machine. There are impact crushers with mounted and fixed hammers. This equipment is classified according to the number of rotors (single rotor and double rotor), the location of the hammers in the rotors, or the direction of rotation of the rotors.
The size of the finished material is controlled by the speed of rotation and the distance (gap) between the hammers and the baffle plate. Impact crushers can have 3-4 crushing chambers.
Having passed through them, the material is unloaded on the conveyor and removed for further processing.
Advantages of modern impact crushers for mining and processing plants:
• High degree of crushing with lower energy consumption per unit of production.
• Simplicity and compact design combined with compact dimensions and low weight.
• Possibility of full automation of the processing line.
Impact crushers are of interest to customers because a high degree of crushing allows them to be used simultaneously at several stages of the technological process.
Also, impact destruction of particles followed by screening significantly improves product quality.
Significant disadvantages of this equipment are the rapid wear of the working parts of the machine, especially when grinding abrasive materials. This reduces the downtime of the crusher between services. For impact crushers, there is a need for high-precision balancing of rotating equipment.
Disintegrators for medium crushing
Disintegrators are widely used in the silicate industry for fine and medium crushing of brittle materials with relatively low hardness and abrasiveness, such as kaolin and limestone.Particle fragmentation is achieved as a result of powerful repeated blows applied to the material by large pins of two rotating rotors in opposite directions.
The rotors are mounted on two separate shafts with independent drive. Each rotor has multiple rows of pins in concentric circles. The material to be ground is fed through a hopper onto the inner row of pins. After the first impact, the partially crushed material falls under the large, counter-rotating pins in the second row.
Thus, successively moving from one row to another, the material is finally crushed and collected at the bottom.
The obvious advantage of this equipment is the fine, uniform crushing of the ore. The disadvantages of the disintegrator include the rapid wear of pins, the difficulty of replacing them and the need for accurate balancing of the rotating parts of the machine.
Engineering design of grinding equipment
After the crushing process, the ore is ground. In addition to achieving a certain granulometric composition, grinding in special mills has as its task to prepare material for beneficiation.When designing mining and processing plants, ore grinding can be developed as an autonomous process or can be included in a closed cycle with crushers and screens.
Mechanical and jet mills
According to the technology used, the mills are divided into two main groups:• Mechanical mills that grind material with grinding media.
• Jet mills that work without grinding media.
In mills of the first type, grinding is carried out by the shock-crushing action of the grinding medium (balls, rods, pieces of ore or gravel) while the mill drum rotates.
There are two main modes of operation, depending on rotational speed, internal diameter and other factors. As the angular velocity increases, the point of separation of the grinding media and material from the drum surface rises higher and higher, forming a continuous layer.
Also, mills can be single-chamber or multi-chamber. In multi-chamber mills, the drum is divided by meshes into separate chambers, in which grinding media of different sizes are placed. The material enters the first chamber and is crushed by the impact of large balls. From here it passes through the grates to the next chambers where the grinding media are getting smaller and smaller.
In each case, the type of grinding equipment is selected individually, depending on the properties of the ore being mined.
Wet and dry grinding
Dry grinding is selected when the resulting material is used in a dry state.Wet grinding is characterized by lower energy consumption and about 15% higher productivity compared to dry grinding. In addition, working conditions are more hygienic and the classification of crushed ore is more efficient.
Dry grinding, in turn, is characterized by a lower consumption of grinding media; there is no need to dry the finished product. Grinding in these machines can be performed intermittently or continuously as part of an open or closed cycle.
Ball mills
Ball mills are widely used in medium to fine grinding of ore.There are several types of this equipment, the most common of which are cylindrical ball mills. Grinding here is continuous and is carried out in a closed cycle. After processing, the product is separated, and the coarse fraction of the material returns to the technological cycle. The mill is driven by an electric motor through a V-belt transmission.
In grate discharge mills, a steel or rubber mesh is attached to the discharge side of the drum.
The role of this mesh is to retain large pieces of rough material and steel balls. The grate sections are attached to radial ribs that divide the space between the grate and the cover into sectors that are open to the discharge opening.
As the mill rotates, the ribs lift the crushed material and discharge it.
Thanks to the mesh, the slurry level is low and the processing time in the mill is reduced. This provides significant benefits, including better use of ball energy and faster material flow through the drum, resulting in even grinding.
Conical ball mills
Conical mills have several features.The largest balls are loaded into the base of the cone of the mill with the largest diameter.
As the taper tapers, the balls get smaller, which ensures optimal ore grinding all the way. The inner surface of the mills is lined with a hard coating cast from manganese steel.
In closed circuit dry grinding, the material supplied by the dispenser enters the drum through the hollow shaft. At the same time, the fan blows air through the hollow shaft, entraining small particles inward. Here the air slows down, while the largest particles are separated and returned to the mill.
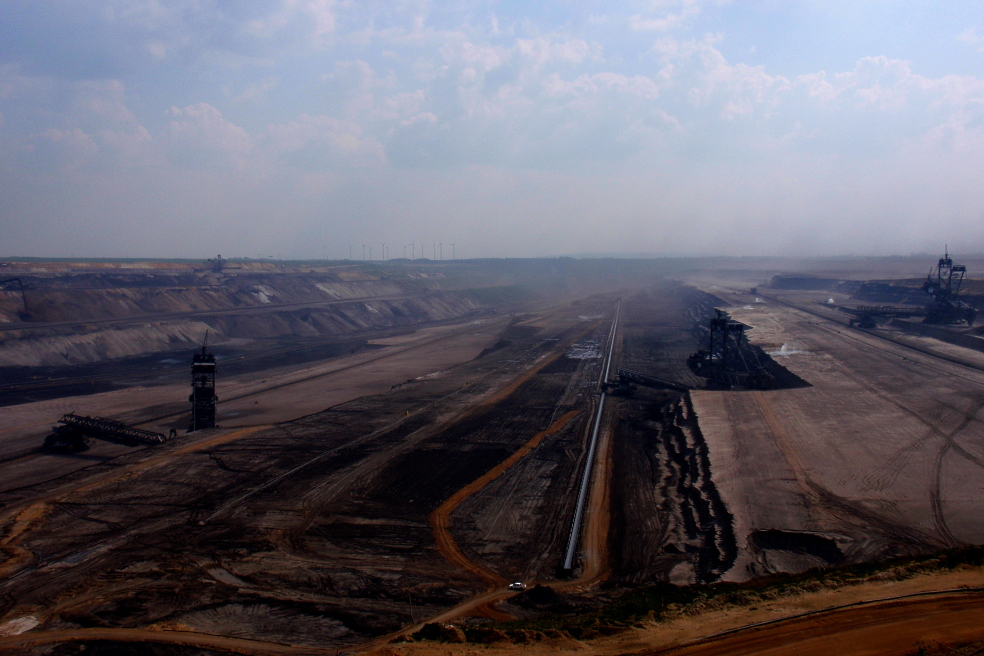
Vibrating ball mills
Vibrating ball mills are sometimes used in the engineering design of mining and processing equipment for fine grinding.In these mills, the drum does not rotate, but vibrates at a high frequency. This makes the small steel balls placed in it move quickly. Due to the frequent collisions between the balls and their crushing action, the material grinds relatively quickly and finely.
The drum is usually round or oval in shape.
Depending on the operating principle, there are eccentric vibrating ball mill and inertial ball mill. Vibrating ball mills are used for all grinding methods, including dry and wet, batch and continuous, open and closed cycle.
Rod mills
Rod mills are structurally similar to center discharge ball mills.There are machines with central discharge, side discharge or center peripheral discharge. They can be used for wet grinding, but peripheral discharge mills are also used for dry grinding. The grinding medium consists of steel rods that are shorter than the internal length of the mill.
These mills differ in that they can handle a large amount of material and the grinding efficiency is high. Large particles absorb the impact of the rods, while small particles are not crushed. Therefore, they are used for one-stage coarse grinding. Rod mills are installed for grinding ore, coal and other wet and dry applications.
Colloid mills
In cases where material grinding must be very fine (less than a millimeter), engineers include colloidal mills in the process.The size of the largest particles of the crushed material in these installations is from 1 to 0.4 mm. This equipment is also used to prepare colloidal suspensions and homogeneous solutions.
Grinding of material in colloid mills is carried out by friction or impacts, wet or dry. These mills usually operate in a closed cycle, with the slurry processed until the desired fineness is achieved. Wet grinding is the most common and affordable method for preparing colloidal solutions.
Centrifugal colloid ball mills are used for fine dry grinding of colloids.
They are loaded with a huge number of balls with diameters of several millimeters. When rotating rapidly, the grinding media are ejected by centrifugal force onto the periphery of the working chamber, where it mixes with the material being processed.
Dry milling looks simple, but it does not produce colloidal particles that are fine enough.
Jet mills
Jet mills for mining and processing plants are aerodynamic grinders, in which the grinding process is carried out without a grinding medium, by impacting particles into each other. Jet mills have a vertical or horizontal working chamber.They also differ in the number of injection devices, the method of dividing the finished product and other parameters.
Equipment for ore separation by screening and classification (sizing)
The mechanical separation of mixtures of materials with different particle sizes, known as screening, is widely used in the mining industry and in the manufacture of aggregates for construction.Depending on the purpose, screening operations can be preliminary, auxiliary or independent.
In preliminary processes, ore is preliminarily divided into classes that undergo various beneficiation operations. Auxiliary screening is aimed at separating particles of the required diameter from the total flow.
The screens consist of a screening surface, a frame on which the screen is mounted, and a drive mechanism. The key requirements for screens are chemical inertness, so that they do not enter into chemical interaction with the screened material, as well as increased mechanical strength of parts and high wear resistance.
The most commonly used screening equipment in the engineering design of mining and processing plants:
• Screens made of sheet metal with different hole sizes.
• Screens made of wire, which consists of high-strength steel and non-ferrous metals.
• Screens consisting of a complex system of rods and roller screens.
In addition to the standard screen types, rubber or polyurethane stretch meshes with high wear resistance are available today.
Each project requires an individual approach to the selection of screening equipment, since the ore grain size and material properties can vary significantly.
The location of the screen holes and their number have a huge impact on screening efficiency. The placement and movement patterns of the sieves are also important. They can be placed in series, parallel or in combination.
Combined (modular) sieve placement to some extent combines the advantages of the first two methods and is considered universal.
Ore screening technologies
Screening is performed in several ways.When sieving from coarse to fine material, the sieves are mounted one under the other, from the largest to the smallest holes. This method provides good screening efficiency and results in slower wear on the working surfaces, but significantly increases the height of the equipment.
The screening efficiency is calculated as the ratio of the mass of the screened product to the mass of material of the same size contained in the raw material for the operation.
Screening efficiency in industrial environments using modern screening systems typically ranges from 85 to 95%.
In some systems, the efficiency can exceed 99%.
When setting surfaces from smallest to largest holes, screening is performed from fine to coarse material, which results in lower screening efficiency and faster screen wear, but reduces the height of the equipment. Combined screening avoids some of the drawbacks of the two described methods, but it is technically difficult to perform and therefore is used relatively rarely at mining and processing plants.
Machines with movable individual elements on a screening surface are known as mobile screening systems. These include roller screens, the rattling surface of which is parallel rollers, on which circular or shaped discs are mounted. Roller screening systems are mainly used for screening non-metallic ore, including coal, shale and anthracite.
Oscillating screens can be inclined and horizontal.
Horizontal machines make differential motion, causing material particles to bounce and move.
As a disadvantage of such systems, experts point out the presence of significant vibrations that are transmitted to the foundation of the building.
Rotary (drum) screening equipment is also used. Its principle of operation is based on the rotational movement of a drum consisting of several sieves. The drum shape can be cylindrical or polyhedral. Special rotary machines with cylindrical screens are widely used for screening materials with different fractions.
Vibrating screening systems
Depending on the type of applied vibrations, vibration systems can perform circular, rectilinear or combined vibrations.The screening surface forms a different horizontal angle, usually from 5 to 30 degrees. Inclined systems are almost always single, while horizontal vibration systems are often combined in pairs.
The following vibrating screening systems are most widely used in the mining industry:
• Eccentric systems. In eccentric systems, the surface of the screen performs circular reciprocating movements as a result of the rotation of the crankshaft.
• Inertial systems. Inertial screening systems are widely used in concentrators. Here, oscillations are created by inertia, and the amplitude of oscillations is variable.
• Self-balancing systems. Self-balancing screening systems are characterized by rectilinear vibrations transmitted from the vibrator to the plane of the screening surface at an angle, so the equipment does not require tilting. This type of equipment is highly efficient.
• Resonant systems. The principle of operation of these systems is based on the phenomenon of resonance. Resonant screening systems are used to dewater coarse and fine coal or some light ores. They are characterized by high efficiency and productivity, as well as low energy consumption.
Other types of vibrating screens are also used in the mining industry.
For example, electro-vibration screening systems, where vibrations are generated by an electric vibrator and transmitted to the body. Their oscillations are strictly rectilinear and parallel to the supporting surface of the frame.
Separation of material by classifiers
In addition to mechanical screening, hydraulic or pneumatic separation of materials into classes is used.Each class of material consists of particles of different sizes, but with the same falling speed of particles in a liquid or gaseous medium.
The process is based on the use of differences in the trajectory of movement of various mineral particles under the influence of gravity, resistance of the medium, the conditions of their fall and the force of inertia. Depending on the medium, the classification can be hydraulic or pneumatic.
Most often, the process occurs in vertical or horizontal air flow. This technology is used to separate mineral particles ranging in size from 5-10 mm to 10-20 microns. Classification is a preparatory process, but with a large difference in the density of separated particles, partial gravity concentration of the ore also takes place.
Similar to the mechanical sorting process, the classification of ore can be done as a preliminary, separate or auxiliary operation.
Pneumatic classification is widely used in dry grinding cycles for non-metallic minerals, as well as for pulverized fuel production and dust removal.
The pneumatic classifier divides the material into large and small particles, and the size of the finished product varies in a very wide range from 1-2 mm to 0.05 mm.
Hydraulic classifiers, depending on the design features and the principle of operation, are divided into chamber, conical, mechanical and centrifugal (hydrocyclones). Separation of fractions using hydrocyclones is a common technology in mining and processing plants. In these installations, separation is carried out in a centrifugal field with significant particle acceleration.
Mechanical classifiers include spiral, paddle and cup classifiers. The separation of small particles from large ones is carried out in the bath, while the sand is removed from the bath using spirals, paddle conveyors or other mechanisms.
Spiral classifiers are the most widely used of all types of mechanical classifiers.
Equipment for the concentration of minerals
After crushing, grinding and screening, which we discussed above, the resulting materials go through various phases of separation and concentration, depending on their properties.In the engineering design of mining and processing plants, several technologies and types of processing equipment are used.
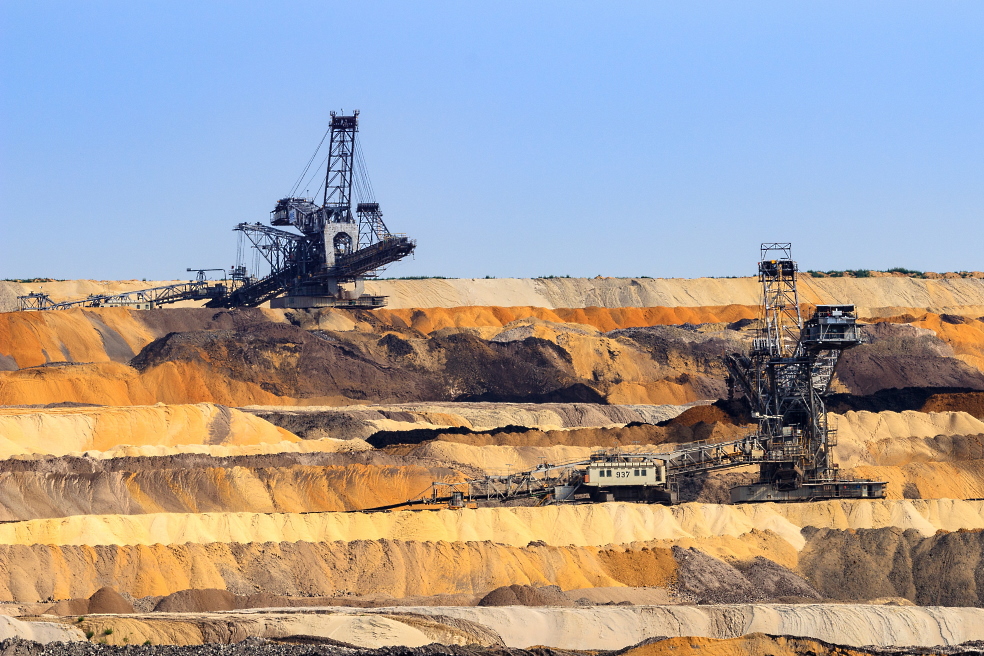
Among them is the gravity method, which uses the difference in density, size and shape of minerals, that is, the difference in the speed of falling of mineral particles and rock.
This process is carried out in a liquid or gaseous medium, divided into hydraulic and pneumatic methods. The hydraulic method is widely used in the beneficiation of coal, iron, manganese, tungsten, tin, rare and precious metals. The pneumatic method is mainly used for coal beneficiation.
Some types of mechanical separators used in the mining industry:
• Wheel separators. This equipment is mainly used for coal. During the separation process, the material passes through a tank filled with a heavy slurry. Inside the working compartment, the material is divided into light and heavy fractions. The light fraction goes to the sieve and is discharged. The heavy fraction is separated as waste by an elevator.
• Drum separators. Drum separators are used to separate large ores. The drum is filled to a certain level, and on its inner side there is a spiral for transporting a heavy fraction. The light fraction flows through the chute and the heavy fraction is discharged through the elevator.
• Cone separators. Cone separators are used for medium-grained ores or non-metallic raw materials. They are a conical bath into which material is fed through a chute. The stability of the suspension is maintained with a stirrer. The light product is discharged through the chute, while the heavy product is discharged by an internal airlift.
• Screw separators. This equipment is used for the beneficiation of raw materials with small particle size. They are intensively used to extract gold from gold-bearing sands, rare metals, tin, weakly magnetic iron minerals, to extract heavy metals from waste, etc.
Magnetic separators
The magnetic enrichment technology is based on the difference in the magnetic properties of the components.Enrichment takes place in a magnetic field generated by magnetic separators.
When a mixture of minerals with different magnetic properties moves through the working area, the minerals with better magnetic properties are attracted by the magnetic field and separated as a magnetic fraction, while the rest of the materials are concentrated as a non-magnetic fraction, subject to further processing.
Some magnetic separators provide for the separation of several fractions that differ in magnetic properties. The terms magnetic and non-magnetic fraction are relative terms. When a raw material is exposed to a weak magnetic field, only highly magnetic materials are released in the form of a magnetic fraction, while a number of weakly magnetic and non-magnetic materials remain in the non-magnetic fraction.
After re-passing the non-magnetic product through the separator under a strong magnetic field, most of the weakly magnetic materials are released. Along with the magnetic forces of attraction, mechanical forces act on the material, determined by the mass of mineral particles, the trajectory of motion, the resistance of the medium, the forces of adhesion, etc.
At present, when designing mining and processing plants, different separators are used for dry and wet magnetic separation for high and low magnetic ores.
The magnetic method is widely used in the following areas:
• Beneficiation of iron, manganese and chromium ores.
• Regeneration of magnets and ferrosilicon suspensions.
• Beneficiation of metallurgical products and rare metal concentrates.
• Separation of tin-tungsten concentrates, etc.
Flotation equipment
The flotation method is based on the use of various physicochemical properties of the mineral surface and the ability of particles to attach to the separating surface of the liquid and gaseous phases.The degree of particle hydration is controlled by flotation reagents. The material is ground in an aqueous medium and, together with the reagents, is fed into the flotation machine.
Poorly wetted particles during this process adhere to air bubbles and separate as a foam product, while rock particles are removed. This is a fairly effective, technically simple and affordable process, which is used by many enterprises in the mining industry and other areas.
Today, mechanical flotation machines are the most widely used. In addition to mechanical flotation machines, engineering companies offer pneumatic, pneumatic mechanical machines and flotation columns.
Sedimentation equipment
Sedimentation is a gravitational process during which minerals are separated by density in a stream of water at a variable rate.This technology is used for coal, as well as for iron, manganese and many other ores with a particle size of 0.1 to 50 mm.
The mineral mixture is layered in two ways.
The first method is applicable to mixtures of two minerals of the same size and different density. When the piston moves downward, an upward jet of water is created, and light particles are carried upward and located in the upper layers of the material. When the piston moves upward, a downward flow of water is created, with the heavy particles moving downward.
Movable sieve sedimentation machines are also available, which are used for the beneficiation of iron and manganese ores.
In these installations, the grating mounted on the bottom makes oscillatory movements under the action of an eccentric mechanism. The movements are arched, as the vertical movement loosens the layer of material on the grate, while the horizontal movement promotes the movement of the material to the unloading side of the installation.
Membrane sedimentation machines are suitable for fine ore particles with or without preliminary classification.
This type of machine has an upper, lower and lateral membrane arrangement.
In the process of operation, the water receives vibrational movements from the pulsation of the membrane and thus stratifies the processed material.
The choice of equipment for the separation and concentration of minerals is based on the properties of the ore, the requirements for the quality of the products produced and many other factors, including the customer's budget. Our experts guarantee an individual approach to each project to achieve maximum results.
Financial and engineering services for mining and processing plants
SI, with the assistance of partners, implements projects in the field of mining engineering of any scale.We offer financing and engineering design of mining and processing plants and the construction of a mining and processing plant under an EPC contract.
Thanks to close cooperation with leading equipment manufacturers, SI is ready to offer the most advanced solutions for the extraction and processing of metallic and non-metallic ores for your business.
Engineering services include:
• Development of a business plan and feasibility study.
• Site selection and negotiations on its use with local authorities.
• Conducting geological, hydrological and other research.
• Engineering design of a mining and processing plant and its infrastructure.
• Preparation and approval of a complete package of technical documentation.
• Organization of tenders and purchase of modern equipment for your project.
• Delivery and professional installation of equipment.
• A full cycle of construction work in accordance with international standards.
• Testing, start-up and trial operation of the mining and processing plant.
• Service and support at any stage of the project.
• Training and supervision of the customer's personnel.
• Modernization and expansion.
Our experts provide customer support in many countries around the world, expanding the geography of SI every day.
If you are interested in financing and construction of a mining and processing plant under an EPC contract, contact our representatives and request a consultation.
We are always ready to share professional experience and offer fresh ideas for your business.