To consider an application for financing, fill out the form and send it to us by e-mail along with the project brief, or contact our experts
In many developing countries, as well as in Eastern Europe, the problem of modernization of obsolete equipment requires significant funding.
The technologies used for the transmission and conversion of electricity have evolved significantly over the past 30 years, and now electrical substations and power lines require a fundamentally new approach to design, construction, maintenance and operation.
Business today is looking for more acceptable technological solutions for the modernization of physically obsolete electrical systems.
Customers from dozens of countries around the world are showing an increased interest in the engineering services of our company, turning to our specialists for the modernization of electrical substations and power lines, as well as for personnel training and maintenance of modern equipment.
We have successfully implemented energy projects with partners in such countries as Mexico, Bolivia, Argentina, Peru, Brazil, Oman, Egypt and Poland.
A high-quality and well-thought-out modernization of the electrical system increases reliability and extends the life of the equipment by at least 20-25 years.
As a result of the successful implementation of an individual set of measures, the customer significantly reduces maintenance costs and equipment downtime associated with breakdowns.
In recent years, the requirements for substations have changed significantly, due to the introduction of alternative sources and changes in the energy structure. Multi-billion investments have been planned around the world to improve the productivity, efficiency and safety of substations.
Generally, the modernization concept includes measures for replacing components with new ones and updating existing equipment. These actions optimize the technical parameters of the system, as well as increase its stability and reliability.
It is assumed that a partial modernization of the medium voltage system (MVS) at substations is economically viable at costs up to 60-65% of the cost of new equipment.
It should be borne in mind that substations are composed of components with different lifetimes and different upgrade / replacement costs.
During the retrofit, our engineers will plan to replace both fixed components (cabinets, current and voltage transformers, insulators, busbars, other slowly aging parts) and moving components, including circuit breakers or disconnectors. The latter are exposed to electrical arcs and their drives wear out quickly as a result of mechanical stress.
In addition to physical aging, switchgears are subject to rapid obsolescence. New types of circuit breakers are emerging that are smaller and lighter and have better performance. Modern equipment is distinguished by an increased switching and mechanical resource, the absence of harmful substances, the minimum need for maintenance and high safety.
Some equipment, such as protection relays, monitoring and alarm systems, become obsolete much faster than they reach their service life limit.
Modernization of distribution transformers, which are responsible for a significant share of electrical losses at the substation, opens up huge opportunities for the investor.
Electric substation modernization project: stages and scope of work
Each customer has his own vision and goals of modernization, which are associated with the characteristics of the services provided, the current market situation and many other factors.We always proceed from your wishes, developing strictly individual projects.
Defining project goals
The goals of the project for the modernization of the electrical substation are determined individually, depending on the state of the existing infrastructure, the customer's requirements and the current rules and regulations for the operation of electrical systems.The overall goals are usually to increase the throughput, safety and reliability of equipment.
As part of this set of measures, it may be necessary to build an additional substation (which means expanding the facility), replace outdated equipment of the existing substation, install modern automation equipment, and remote monitoring and control systems.
Feasibility study
Feasibility studies and calculations can be carried out locally, regionally and nationally.These works involve a detailed analysis of the technical aspects of the project, an assessment of costs and financial risks, as well as forecasting the impact of the project on the environment and the local community. These studies require the involvement of a wide range of specialists from different fields who are able to analyze all possible aspects of the project.
For example, a transformer installed in an existing substation may reach its capacity limit. Such equipment slows down the economic development of the region and of the enterprises that consume energy from this substation. Failure to complete the modernization increases the risk of power outages, which affects all stakeholders.
Justification for the selection of the site for the expansion of the substation
When planning modernization, the impact on the environment, building boundaries and other factors are taken into account.If the current size of the land does not allow for expansion of the substation according to the design or access to heavy machinery to accommodate equipment, negotiations with the local community on the expansion of the site are necessary.
SI with partners can assist the customer in buying or leasing land that meets the technical, environmental and economic conditions — proximity to access roads and power lines, sufficient area to expand the substation, insignificant vegetation cover, etc.
Based on the customer's requirements, current regulatory documents and national standards, the engineering company develops a complete package of technical documentation for the project. A detailed plan for procurement, equipment delivery, construction and installation work, testing and commissioning of the facility is also drawn up.
If the project involves the expansion of an electrical substation or the construction of additional facilities near an existing facility, we conduct a full range of site surveys, including soil surveys, topographic surveys, and so on.
Specialists will accompany the customer at every stage of the implementation of the substation modernization project, providing advice on demand. We are ready to deal with obtaining official permits and negotiations with third parties, as well as carry out other responsible and time-consuming procedures.
Construction and installation work
The specific list of preparatory, construction and installation work for the modernization of equipment and the expansion of electrical substations varies depending on the project.Typically these services include the following:
• Preparation of the substation: dismantling of old equipment and structures, clearing the territory for the expansion of the facility, excavation and leveling of the ground, waste disposal, preparation of storm sewers and other infrastructure, installation of temporary structures for construction work.
• Delivery of heavy construction equipment, tools and materials to the construction site, as well as accommodation of personnel who will be involved in the work.
• Purchase, delivery, assembly and testing of electrical and electromechanical equipment intended for modernization, as well as the organization of the proper storage of this equipment at the construction site.
• Сonstruction and installation of equipment, followed by testing and commissioning.
Our company offers financing and engineering services under an EPC contract, implementing the project from A to Z. We take full responsibility for the planned work, acting as the only contact person for the customer.
Investment in smart power distribution networks
The modernization of electrical substations and power distribution networks is now inextricably linked to the development of smart technologies.The move to smart grid infrastructure can help utilities solve many challenges. Although investment in smart grids has grown by 5-15% annually over the past 5 years, it still represents a small proportion of total investment in the energy sector.
Despite the initial enthusiastic response to smart grids, there are a number of technical and financial challenges. In addition, further efforts are required in some developing countries to implement a regulatory framework that recognizes and encourages investment in new digital technologies and other “wireless” alternatives to traditional power grids.
The significant increase in electricity generation from renewable sources in Europe has great benefits for the global climate.
Today, 20% of electricity in the EU is generated from renewable sources.
The good news is that some countries are working harder. For example, Denmark has long crossed the 50 percent threshold for renewable energy production, mainly from wind power.
However, unpredictable production creates fluctuations in electrical grids, as most of the green energy is generated only during the period when the wind blows or the sun shines. Typically, the production of wind power does not match the periods of peak consumption.
Therefore, their capacities are either too high or insufficient.
In addition, some renewable sources only supply medium and low voltage networks, which are not subject to constant monitoring (unlike high voltage networks). Therefore, there is a lack of information about the electricity supplied to these distribution systems.
In the past, energy consumption was stable and predictable. Due to fluctuating energy costs and growing environmental concerns, consumers are changing their energy consumption behavior. Currently, the problem is not only unpredictable production, but also fluctuations in consumption.
As a result, it is becoming increasingly difficult for utility companies to maintain the reliability of their distribution system.
This is a key parameter in avoiding power outages.
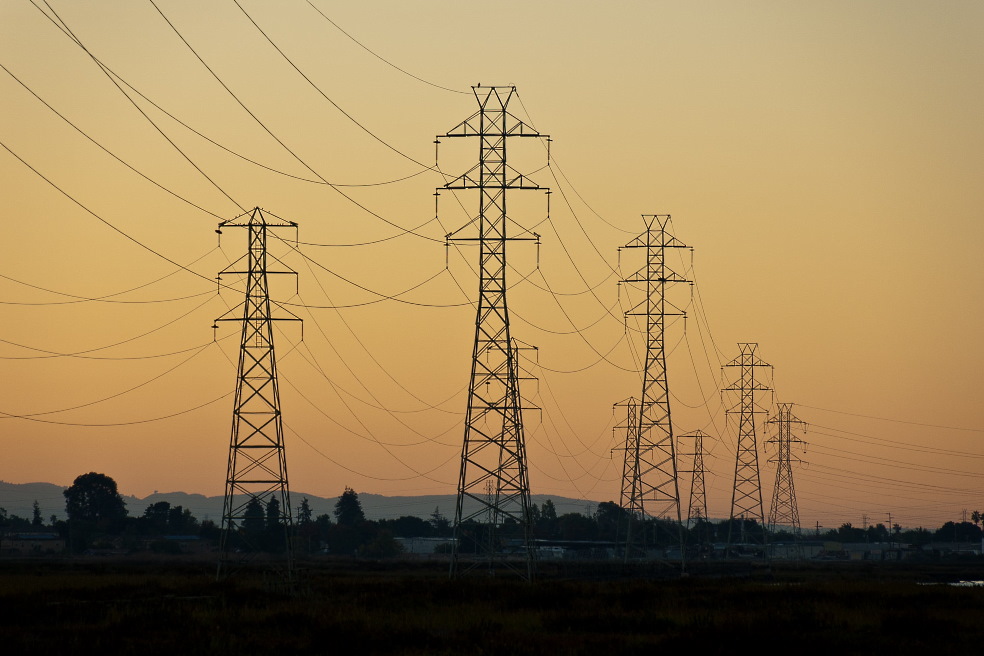
New opportunities for modernization of power grids and substations
One way to increase profit for companies is to economically store electricity in batteries across the network to cover local peaks.This is a tremendous opportunity to optimize the power distribution system, especially in countries facing unpredictable green energy generation.
Modern technologies are making it possible to modernize the analogue power grid with the help of computerized solutions and digital communications. As a result, an infrastructure is created that is capable of processing large amounts of data and managing high capacities as efficiently as possible.
This improves the power grid in several specific areas:
• More possibilities for monitoring. The equipment is approaching the point where it can get a complete picture of the state of the network. This also means that it can transmit sensor data in real time more efficiently.
• Effective control. Computerized systems can bring an electrical system to any desired state with minimal human intervention.
• Higher degree of automation. New technologies are helping companies adapt to rapidly changing consumption conditions.
• Enhanced integration. Connecting isolated systems and processes can provide additional business benefits.
Utilities in United Kingdom, Denmark, Germany and several other countries are already benefiting from the introduction of modern digital equipment and communication systems that private engineering companies develop on individual projects.
They are designed for specific electrical equipment and meet all applicable industry standards and specific operating conditions.
The industry's main focus is on power distribution networks and substations.
These links are especially important because they link power generation centers and end users.
Electrical substations and power distribution networks must accept different types of traffic for different functions, including operational and control communication with SCADA, and more. The modernization is based on the following three main characteristics: redundancy of generated power, built-in security, and upgradeability to support multiple communication types.
The most advanced solutions available to businesses and utilities can help reduce substation operating costs by improving reliability and optimizing distributed energy integration.
Operational centers are a key point for analyzing data flowing into the smart grid.
The software at these centers performs many functions, ranging from fault detection to maintenance scheduling.
A key feature of the operational center modernization is to ensure fast and accurate delivery of data from smart devices to the appropriate applications and to respond to malfunctions and fluctuations in operating parameters in real time. New technologies and services aim to provide solutions for advanced data collection, rapid analysis and response to any power system problem.
The vision for the future must include the use of technology to transform the way we meet energy and environmental challenges and create a secure global power distribution network.
This requires the following conditions:
• Maximize the convergence of service systems and workflows for all key elements of the smart grid in order to increase its intelligence and ultimate efficiency.
• Providing innovative technical solutions using security platform based on open standards.
• Ensuring network reliability, security and flexibility, better power quality.
• Fast and secure communication between components.
Power generation and distribution companies face countless dilemmas today.
Substations and power lines are becoming obsolete, the traditional one-way model is losing its relevance due to a decrease in the level of safety, the patterns of energy consumption and power generation are changing.
At the same time, consumers want to pay less for electricity, they expect more reliable devices, more transparency about their consumption patterns and more choice of energy sources.
Regardless of geographic location, businesses, government agencies and utilities are massively adopting smart grid strategies and smart communications infrastructure that can effectively integrate all elements of energy consumption and generation into a modern energy system.
Automation of electrical substations with SCADA
The engineering company has extensive experience in the automation of electrical substations of any type.During this time, we have successfully implemented many projects using equipment from leading European manufacturers. This allowed us to gain in-depth specialized knowledge of automation and control systems in electrical substations with various communication protocols and control strategies.
Our engineers provide a full range of professional services in the field of automation of new substations and modernization of existing facilities. Our experience and an integrated approach to project management allow us to offer optimal solutions tailored to your project, which guarantee future scalability of the system.
We carry out the following substation automation and monitoring works:
• Design and update of communication and control architecture.
• Basic and detailed design of equipment for electrical substations, manufacture and installation of automation and telecommunication systems.
• Installation and configuration of gateways, protection relays, controllers, data concentrators, alarm panels and meters, as well as their integration with the SCADA and HMI systems.
• Installation of SCADA system and other high-tech equipment, setting up the HMI graphical interface for optimal display of events, etc.
• Testing and commissioning of automation and control systems for electrical substations.
Automation and control systems provide operators with a complete picture of the internal state and behavior of electrical networks.
This equipment helps to reduce costs, improve operational reliability and simplify the detection of power system problems.
Modernization of distribution transformers: options and opportunities
Modern distribution transformers are becoming more efficient than ever before and at the same time more cost effective.Market reality shows that amorphous technologies can be even more efficient and affordable. Total cost of ownership and life cycle cost are important factors that investors consider when choosing a specific piece of equipment.
One of the obstacles to reducing transformer losses in power distribution companies is the changing regulatory environment. In developing countries, it changes too often compared to the payback period for investment in electrical infrastructure.
In order to take the first decisive step in improving the efficiency of transformers, it is necessary to remove the existing obstacles in the current legislation. Additional incentives should be introduced to encourage investment in energy efficient transformers.
The issue of modernizing electrical substations is associated with the choice of the optimal type of transformer that best meets the needs of the customer.
The world's leading manufacturers of transformers for electrical substations:
Manufacturer | Country |
GE | United States |
Siemens | Germany |
Mitsubishi Electric | Japan |
Schneider Electric | France |
ABB | Switzerland |
Transformer manufacturers offer many options.
Our customers have access to sufficient information about the operational and economic parameters of the transformer to make a rational decision when choosing a specific type and model of equipment.
Investing in a state-of-the-art, energy-efficient transformer means reducing energy losses and minimizing negative environmental impacts, as well as dramatically reducing the cost of the product's life cycle and therefore increasing profitability.
How to reduce energy losses in transformers
Transformer losses can be divided into two main types - no-load losses and load losses.These types of losses are typical for all transformers, regardless of their application or power. However, there are two other types of losses — additional losses caused by harmonic currents and cooling losses caused by the use of cooling equipment such as fans and pumps in high power transformers.
No-load losses occur in the magnetic circuit of the transformer whenever a voltage is applied to the transformer — even when its secondary winding is open. They are also called magnetic losses and are permanent.
These energy losses consist of hysteresis losses and eddy current losses.
Hysteresis losses are caused by the friction of magnetic fields in the layers of the magnetic circuit, which are magnetized and demagnetized by changing the magnetic field.
These losses depend on the type of material used to manufacture the magnetic core. Silicon steel has much less hysteresis than conventional steel, but amorphous metal alloys give significantly better results than others.
Hysteresis losses are usually responsible for more than half of no-load losses (50-70%).
In the past, this ratio has been lower due to the higher relative percentage of eddy current losses, especially in thick, untreated sheets. Nowadays, hysteresis losses can be reduced by processing materials using cold rolling, laser processing and reorientation of grain structure.
Eddy current losses occur due to changes in magnetic fields that cause eddy currents in the plates and thus generate heat. These energy losses can be reduced by making the magnetic circuit of thin layered sheets, isolated from each other by a thin layer of polymer, in order to reduce eddy currents.
Eddy current losses are typically 30 to 50% of the total no-load losses of a transformer.
When we talk about measures to improve the efficiency of distribution transformers, the greatest progress has been made in reducing these losses.
There are also dielectric and other types of losses that occur in the core of a transformer, but these usually amount to no more than 1% of the total no-load loss.
Ohmic losses occur in the transformer winding and are related to the resistance of the wire. Losses depend on current and winding resistance. Resistance can be reduced by increasing the cross-sectional area of the conductor or reducing the length of the winding. The use of copper as a conductive material maintains a balance between weight, size, price and resistance; adding more material to increase the wire diameter reduces losses.
The total losses in distribution transformers that are installed in electrical substations in the EU member states are estimated at around 33 TWh per year. However, this figure does not include reactive power losses from harmonics, which add at least another 5 TWh per year for all distribution companies and private distribution transformers.
Consequently, the total losses of distribution transformers in the EU can exceed 38 TWh per year.
Superconducting and amorphous metal transformers
According to a recent study, load losses have decreased by about 30-50% over the past 40 years.Copper conductors have replaced aluminum due to lower resistance and better tensile strength. The design of the conductors has also been improved with the introduction of continuously moving conductors (the conductor is divided into several flat conductors that are regularly moved), which reduces eddy current losses and allows a significant improvement in winding density.
On the other hand, the design of the windings and the improved insulation make the conductor thinner, allow higher temperatures and increase dielectric strength, and reduce load losses.
With regard to losses at idle, their reduction by 3-4 times over the past 40 years can be called revolutionary.
The gradual replacement of hot rolled steel with a more suitable cold rolled steel has been accompanied by significant improvements in materials. Recently, silicon steel is being developed which is characterized by very low losses.
The widespread adoption of laser cutting of metal leads to a decrease in unevenness, improving insulation between the plates and reducing idle energy losses. The plates are thinned to 0.1 mm (typically 0.2-0.3 mm), which further reduces load losses.
In a superconducting transformer, windings made of high-temperature superconducting material (HTSC) are cooled with liquid nitrogen at 77 K, so the resistance is extremely low.
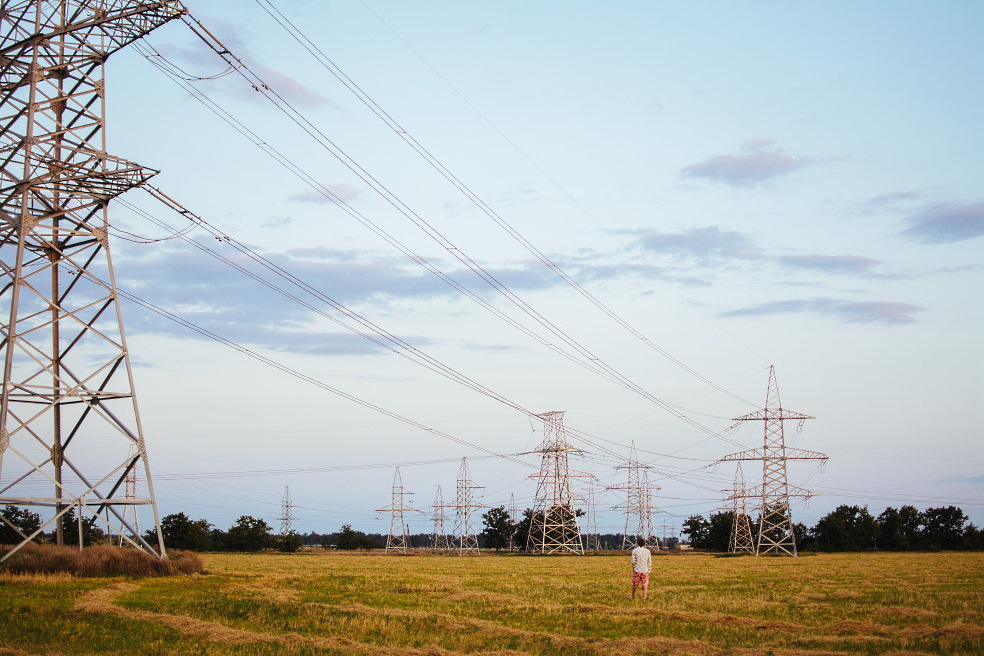
As a result of nitrogen treatment, energy losses can be reduced by 50%.
The use of HTSC transformers on a large scale is economically viable and will become more attractive as cooling systems improve and the costs of liquid nitrogen production decrease. Another important factor is the significant technological progress in the production of long HTSC wires.
Transformers of this type have less weight and dimensions.
They are more resistant to overload, but today they cost almost 150-200% more than conventional transformers. Compact models of forced-cooled transformers can be used for retrofitting facilities where weight and dimensions are critical.
Amorphous alloys differ from crystalline alloys in special magnetic and mechanical properties (hardnessб strength). The market share of amorphous metal transformers worldwide is significant: more than 3 million of them are single-phase and about 1 million are three-phase, respectively.
This represents about 5% of the global market share, but this figure does not apply to the European market. Research shows that the development of the European market is just beginning.
To obtain an amorphous structure in a solid metal, the molten metal must solidify very quickly, preventing crystallization. In this case, the required cooling rate of the molten metal is about 1 million degrees Celsius per second.
In the case of transformer magnetic circuits made of amorphous metal alloys, the efficiency of power distribution in electrical substations is significantly increased by reducing losses. The loss reduction ranges from 65% to 90% compared to silicon steel transformers used in Europe.
Amorphous technology is especially suitable for low-load transformers as it reduces the effect of harmonics on no-load losses. Increasing consumption leads to significantly greater harmonic distortion in power systems. High frequency harmonics lead to increased losses in the magnetic circuits, especially in distribution transformers that use conventional steel magnetic circuits.
Modern distribution transformers with amorphous metal magnetic circuits are extremely beneficial for providing low losses at low load and at high frequencies. This is due to improved manufacturing technologies that allow for thinner and denser metal strips, as well as the amorphous nature of the material, which has higher resistance and allows magnetic flux inversion with low power consumption.
In terms of manufacturing costs, amorphous transformers only have slightly higher or nearly the same prices as conventional high efficiency transformers. SI with partners is ready to offer you any solutions in the field of modernization of distribution transformers at substations and other facilities.
The cost of upgrading electrical substations
In our society, a reliable supply of electricity to consumers is taken for granted.The companies responsible for the supply of electricity to end users are under constant control and inspection on all issues related to costs. The problem of minimizing capital costs can sometimes be compounded by a lack of understanding of end-user distribution of electricity.
According to Global Market Insights, the global electrical substation market will surpass $210 billion in 2026, showing an average annual growth rate of 5.6%.
At the same time, global spending on modernization of substations has already exceeded $38 billion.
The cost of modernization usually does not exceed half the price of new equipment of the same type. With the global crisis and economic slowdown, more and more private companies and utilities are looking to save money by extending the life of existing substations.
This is achieved by upgrading, installing efficient components and replacing worn out equipment.
Such measures can guarantee up to 20-30 years of reliable operation with minimal investment.
The cost of modernization in each case is calculated individually and depends on the planned scope of work, the selected equipment and additional services. For example, the cost of installing new control equipment can be several hundred thousand dollars, but installing a high-power transformer costs from 500 thousand to 3 million dollars or more.
The construction of an additional substation will require tens of millions of investments.
Professional services in the field of modernization of electrical substations
Responsible modernization requires deep engineering knowledge.Taking into account the wide variety of existing distribution systems, including electrical substations at large factories in Europe, we offer an individual approach to customer needs.
Together with our partners, we specialize in the financing and implementation of large energy projects under the EPC contract.
We always practice a responsible and differentiated approach using the latest European technologies and our own know-how.
We offer equipment renewal and installation of the latest systems, including modern high-performance transformers and switches with microprocessor protection. The work of our engineers is focused on achieving the desired result for the client with minimal financial and time costs.
The potential benefits of comprehensive substation modernization include:
• Significant increase in equipment life, usually exceeding 20-25 years.
• Improving the quality of operation (self-diagnostics, ease of maintenance, remote control).
• Ability to perform the entire range of works without stopping the technological process.
• Reduction of energy losses by 2-3 times due to the renewal of buses, insulators, etc.
• Reduction of harmful emissions by 3-4 times compared to obsolete equipment.
• Improving the overall stability and reliability of the substation.
Investors' knowledge and awareness of the benefits of modern technology are driving global demand for substation and power line modernization services.
It is a cost-effective way to transform obsolete equipment into a progressive, energy efficient and environmentally friendly system.