To consider an application for financing, fill out the form and send it to us by e-mail along with the project brief, or contact our experts
Construction, expansion, modernization and safe operation of LNG terminals is becoming one of the priority areas of our investment company.
The unique properties of liquefied natural gas allow supplying companies to accumulate and store an enormous amount of energy in a small area, guaranteeing consumer safety for a long time. The LNG industry makes it possible to lay hydrocarbon supply chains anywhere in the world where conventional gas pipelines cannot be built.
The construction of liquefied natural gas plants brings a number of benefits to the global economy and especially to the most energy-intensive industries.
These benefits start with significant cost savings and include high stability of energy supply, flexibility and environmental friendliness.
Thanks to the rapid improvement of technologies, the reduction in construction costs and the reduction in the timeframe for the implementation of investment projects, the construction and expansion of LNG regasification terminals has intensified in many countries in recent years.
For example, the European Commission expresses the commitment of the EU member states to move towards a sustainable, competitive and secure energy system.
EU energy legislation focuses on natural gas and electricity markets. Diversifying gas supplies remains a key challenge for Europe. To achieve this goal, the European LNG infrastructure must acquire flexibility and the ability to quickly compensate for changes in energy supplies.
For most developed countries, the LNG market and LNG supply and storage management infrastructure have become a strategic tool to achieve diversification and adaptability of the energy system. We can see this from the growing statistics of completed projects and the rapid increase in investments all over the world.
Sedona Investments, a company with a wide international presence, offers financing and construction of LNG terminals under an EPC contract.
Contact our representatives to learn more about our advantages.
Basics for the construction of LNG regasification terminals
LNG stands for liquefied natural gas, which in liquid form reduces its volume by up to 630 times and becomes extremely convenient for storage or transport. In order to transport natural gas around the world by sea, it is liquefied by cooling down to about -162 ° C.Refrigeration / liquefaction consumes a significant amount of energy, reaching about 20% of the calorific value of the gas.
Liquefied natural gas can be stored for a long time in special multilayer tanks or transported in LNG carriers (tankers) from one terminal to another, where it is finally regasified and supplied to end users through pipelines.
The terminal includes equipment for loading and unloading liquefied natural gas from / to a tanker, equipment for transportation to the liquefaction site (for export terminals). LNG terminals also carry out regasification, processing, storage, pumping, compression and gas metering. Gas liquefaction is currently considered the most efficient way to transport gas over long distances.
Some regasification terminals are onshore, others are floating storage and regasification units (FSRU) with LNG regasification equipment. Floating structures of this kind can reach impressive dimensions and performance.
One of the largest FSRUs in the world is the MOL FSRU Challenger, capable of transporting up to 263 thousand cubic meters of LNG.
As part of the planning of a stationary offshore or onshore LNG regasification terminal, the engineering team can select a GBS (Gravity Base Structure) concrete platform or one of many alternative structures. The choice of the type and design of the LNG terminal depends on the technical, economic and environmental requirements.
Table: Classification of regasification terminals by location.
Category | Structure types |
Onshore LNG Terminals | Traditional LNG terminals, consisting of a pier, pipelines, onshore LNG storage tanks and regasification equipment. |
Offshore LNG Terminals | Located close to the coast, such facilities are being built on a fixed offshore platform to supply gas to consumers onshore through a network of subsea gas pipelines. |
Floating Terminals | This broad group includes regasification vessels (LNG RVs) or floating storage and regasification units (FSRUs) that serve for gas storage and regasification. |
Thus, modern technologies offer businesses ample opportunities for the construction of LNG regasification terminals onshore and offshore.
The essence of the terminal is shown below. Tankers arriving at the terminal pump LNG into tanks, after which gas, depending on the needs of the consumer, is supplied to the evaporation system for heating and converting it into a gaseous state and supplying it through a gas pipeline.
The technically complex regasification process can be carried out directly and indirectly, which determines the choice of equipment for a specific technological chain of a particular terminal.
In the first case, the "hot" coolant (seawater) is in direct contact with LNG, and in the second case, heating is carried out through an intermediate coolant (usually propane gas).
Regasification terminal, regardless of its type and location, includes expensive units and equipment for unloading, isothermal LNG storage tanks, pumps, condensers, flare system, nitrogen generators, metering units, odorizers and much more.
The key requirements for such projects are always reliability, stability and operational safety in any conditions.
A typical onshore regasification terminal occupies a significant area on land and adjacent waters, which are fenced off by breakwaters. This construction site, covering an area of several square miles, includes an offloading terminal, pipelines, tanks and extensive port infrastructure. The creation of such facilities involves long-term engineering and design work, research and coordination with environmental authorities and other regulators.
Due to the extreme complexity and high investment cost, the construction of an LNG regasification terminal requires a highly professional approach involving many contractors with specific knowledge, technologies and experience.
LNG terminal construction stages
The construction of any facility associated with high environmental risks requires official permission based on the results of environmental studies, the safety of personnel and the public.These activities are carried out by specialized engineering companies and construction contractors with experience in LNG and related projects.
Formally, the construction of LNG regasification terminals begins with obtaining official permits, which are issued on the basis of the following:
• Constituent documents of the project company or other legal entity formally responsible for the implementation of the project and associated risks.
• General description of the LNG terminal project and site layout plan with indication of gas intake, storage and regasification zones, nearby settlements and other environmentally sensitive areas outside the site.
• A complete list of technical standards and other documentation that is used by the contractor in the engineering design and construction of the terminal.
• Detailed environmental risk assessment and action plan in case of potential accidents and environmental disasters based on the study of the project.
• An approximate timetable for the implementation of the project, indicating the specific stages of construction and their time frames.
• Other documents required by the authorities of the host country.
The subsequent stages of LNG terminal construction largely depend on the type of facility.
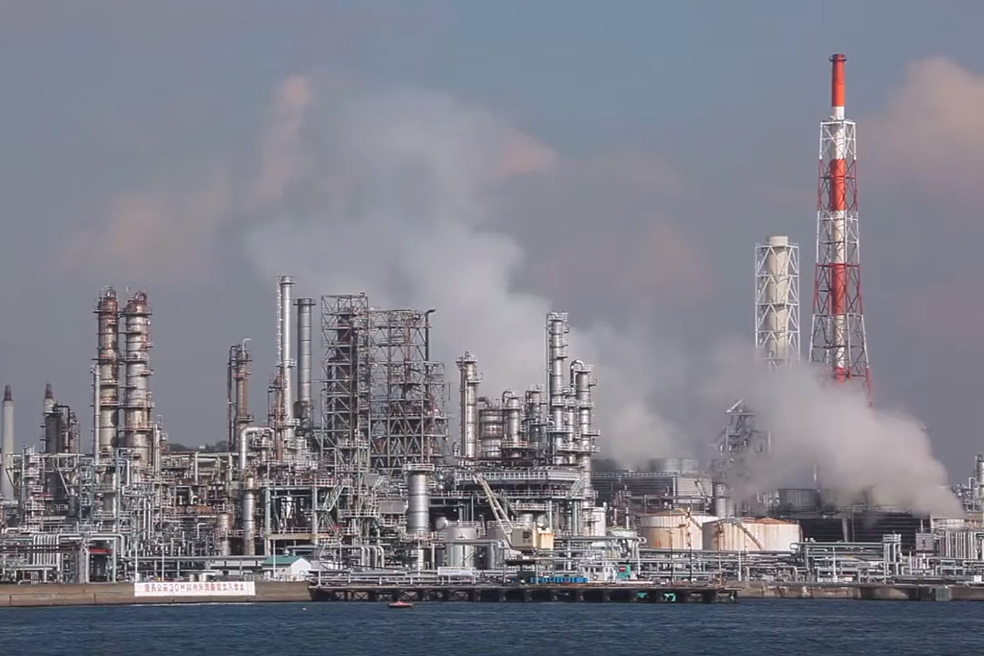
Since in most cases we are talking about onshore and offshore terminals for receiving LNG carriers from abroad, the construction of the facility begins with a detailed study and preparation of the water area and coastal zone for large-scale construction work.
The general contractor and specialized construction companies involved in the project provide site preparation, dredging and fencing of the future terminal's water area, laying high-pressure pipelines, pouring foundations and installing equipment for regasification and gas storage. All work must be carried out under the supervision of certified professionals to ensure the safety of the project and the achievement of the investor's goals.
SI team is ready to provide comprehensive support to the customer at all stages of financing and construction of LNG regasification terminals in any climatic conditions.
One of the main challenges for energy companies is the long and complex process of planning, approving and building LNG regasification terminals. It should be noted that up to 80% of the time is spent on obtaining the appropriate permits.
Our reputable partners are ready to take on the technical and bureaucratic work, including obtaining official permits and organizing the investment process.
With our comprehensive services, your team will be freed up to focus on more important business areas.
The cost of professional services for obtaining permits and organizing the construction process is considered insignificant in relation to the total investment in a medium-sized LNG regasification terminal project. Compare our offers and see the obvious competitive advantages.
Testing, commissioning and safe operation
Liquefied natural gas requires professional handling to ensure safety.Many concerns about LNG are actually myths, but strict adherence to technical standards is critical to any gas project.
On contact with air, LNG evaporates and dissipates, being lighter than air. Potential leakage of gas from tanks does not lead to environmental pollution or poisoning of people, since it is a low-toxic substance. In addition, burning LNG does not generate hazardous ash, unlike coal.
It should also be noted that liquefied natural gas has a high autoignition temperature, making it a safer fuel than highly flammable and explosive petroleum products (such as gasoline).
Testing and commissioning of the LNG regasification terminal is carried out in accordance with a well-known and well-proven algorithm of operations, including pipeline and tank inspections, testing of safety systems and personnel certification. The introduction of reliable sensors and electronic systems for remote monitoring of operating parameters contributes to an unprecedented safety in the operation of facilities.
Thanks to the use of reliable equipment, the introduction of modern telecommunication systems and high-quality personnel training, the availability of regasification terminals in recent years has reached almost 100%.
Before starting the operation of the LNG terminal, the general contractor usually carries out comprehensive training of the customer's personnel (operators, technicians and engineers) who are responsible for the operation and maintenance of the equipment. Although the new systems are highly automated and require minimal human intervention, the role of training in this industry cannot be overemphasized.
LNG infrastructure and equipment
Currently, the infrastructure of liquefied natural gas includes a wide range of costly facilities on the way from the gas field to the end consumer.This chain includes high and medium pressure gas pipelines, LNG plants, methane tankers and regasification terminals on the receiving side.
All this expensive infrastructure requires a multi-billion dollar investment in a short time frame to ensure the efficient and safe operation of such a chain with sufficiently high economic results in the long term. The selection, procurement, installation and customization of special equipment for regasification terminals plays an important role in investment projects of this kind.
Below we have listed some of the technologies and equipment used in the construction of LNG regasification terminals and other elements of the LNG infrastructure.
Liquefaction of natural gas
The commercial LNG cycle begins at LNG plants.To ensure smooth gas liquefaction at -162 ° C, it is necessary to first remove impurities such as heavy hydrocarbons, carbon dioxide and others. In addition, the water content must be reduced to 1 ppm prior to liquefaction.
Floating installations use the so-called nitrogen cycle to remove water, which is an easier and safer way to dehydrate natural gas compared to methods used at land terminals (pressurized heating, centrifugation or high voltage electric current).
Cooling is carried out by heat exchange with one or more substances that lower the temperature. The refrigerant can be propane, propylene, ethylene, methane and others. Liquefaction takes place in several cycles or in one refrigeration cycle.
There are three main types of commonly used gas liquefaction plants. In the first case, the gas is cooled in a cascade cycle using several one-component refrigerants in heat exchangers located in series. In this case, the gas pressure is gradually increased by the compressors. The second type of technology is refrigeration in one cycle with mixed refrigerant.
Sedona Investments is ready to assist you in financing, developing or building the entire LNG infrastructure chain, including liquefied natural gas plants, regasification terminals and pipelines.
Loading and unloading equipment
Upon arrival at the LNG terminal, the tankers dock at the unloading point.Unloading is most often carried out by connecting articulated booms. The liquefied gas is transferred through a pipe system to storage facilities on the territory of the terminal. The operation to unload a tanker today takes at least 1-2 hours.
Liquefied gas pipelines are specially designed to withstand very low temperatures.
Conventional carbon steels are too brittle at such low temperatures, so special metal alloys are used to unload LNG. Suitable materials are aluminum alloys up to 5% magnesium and steels with a high nickel content.
The booms have specially designed pivoting joints to provide the necessary movement between the ship and the terminal equipment. This system also includes a counterweight to reduce the load on the boom on the ship's manifold and reduce the effort required to maneuver the boom.
The range or operating radius of the boom of the unloading terminal is determined by changes in the flow and changes in the freeboard of the tanker during the loading or unloading of LNG.
An alternative to such designs can be high-strength hoses made of low-temperature material with very good insulation. The disadvantage of these hoses is that they are heavy and require additional planning as they move.
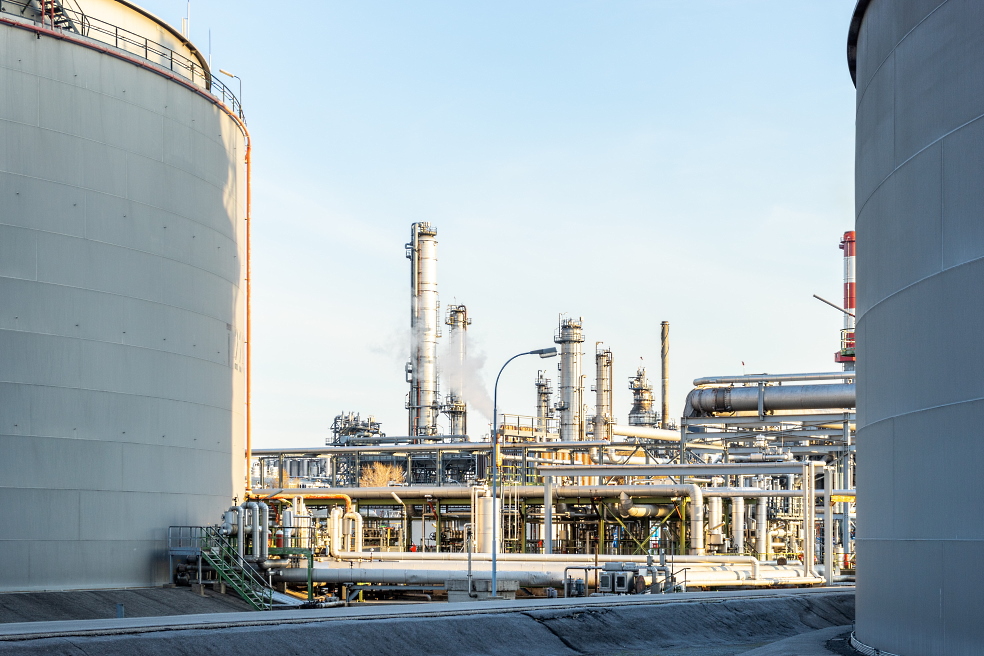
The connection between the unloading boom and the tanker is either flanged bolted connections or a quick connect / disconnect coupler (QCDC) for faster handling.
The connection is done manually, but usually the clamps are tightened and opened with hydraulic traction.
When pumping LNG, the connection is reinforced by a mechanical interlock independent of the hydraulic mechanism. A quick connection can be the best option for personnel safety in seaports where maneuvering is problematic.
Boil-off gas control
Although cryogenic LNG tanks are designed to keep temperatures low, they cannot provide perfect insulation from heat.External heat sources gradually heat up the tanks, which evaporates a small percentage of the liquefied natural gas, resulting in the release of boil-off gas (BOG).
Natural gas remains in a liquid state and is kept at a constant high pressure, but when it boils and turns back into gas, the expansion of the volume increases the pressure in the tank. Although the tanks are designed to withstand significant pressure build-ups for a short time, continuous pressure build-up requires alternative engineering solutions.
The vaporized natural gas is transported in liquefied gas tanks and sent to boil-off tanks.
This gas can then be compressed and connected to the local gas network, sent to a liquefied gas plant, or returned to LNG storage tanks.
Re-liquefaction of the boil-off gas is carried out by cooling. However, this process has some peculiarities that make storage difficult. Gas evacuation requires a lot of additional equipment, so the tanks become very large. This process is more practical for large onshore LNG plants where space is not as much of an issue.
In floating LNG terminals, the problem of gas evaporation is solved by gas flaring. Surplus gas is fed to the ship's engines, which are rated for the appropriate fuel pressure for fuel consumption. BOG can be used as fuel for the ship. Moreover, some tankers rely solely on this type of fuel to perform certain maneuvers.
The construction of LNG regasification terminals requires careful planning of the boil-off gas management system to ensure efficient use of gas and improve the safety of the entire terminal.
Liquefied natural gas storage
Liquefied gas is stored either in a highly compressed state, in a semi-compressed state, or at very low temperatures.At ambient temperature and ultra-high pressure, liquefied gas can be stored in above-ground spherical tanks, buried horizontally located cylindrical tanks or underground storage facilities with multilayer tanks.
LPG tanks must be equipped with high pressure relief valves. Safety valves of different designs are used. Depressurization can take place in both the atmosphere and the incinerator, depending on the quantities stored, the location and the gas. Flame arresters in ventilation pipes can be a potential cause of pipe clogging (which can damage the tank) and should be checked regularly.
The LNG tank is equipped with a water spray system for added protection in the event of a fire.
Alternatively, special coatings are used that char in the event of a fire, providing significant heat absorption and insulation.
Piping and valves used in the construction of LNG regasification terminals must be designed, maintained or installed in strict accordance with technical standards and best practices.
This means, for example, that the inlet and outlet piping of storage tanks must be securely insulated. This piece of equipment for the LNG terminal must also be designed to safely compensate for the thermal expansion of the liquid in the pipelines.
Test points in LNG pipelines are usually equipped with double check valves. The bottom line is to fully open the primary isolation valve and apply gas to the second valve. Thus, any blockage of the pipeline due to the formation of hydrates will occur at the second valve, leaving the primary valve free to isolate the reservoir again until the blockage is cleared.
These and many other safety measures are critical to a modern LNG regasification terminal project, regardless of its type and size.
The installation of gas handling equipment requires the involvement of highly qualified construction teams with rich practical experience and advanced equipment.
LNG regasification equipment
The process of direct or indirect heat exchange between LNG and working fluids is the main technical principle used for regasification of natural gas in most terminals around the world.Currently, the following regasification technologies are widely used:
• Open rack evaporators (ORV).
• Shell and tube evaporators for liquefied natural gas (STV).
• The so-called submerged combustion evaporators (SCV).
• Combined heat systems with submerged combustion evaporators (CHP-SCV).
Other types of evaporators are used for regasification of small volumes of LNG.
Depending on the heating medium, regasification can be carried out, for example, by ambient air evaporation (AAV). Some factories use heat from other industrial processes as a source of energy.
An important LNG regasification terminal construction stage is the installation of a series of heat exchangers, which must pass the gas during its evaporation. Air enters the evaporator and exits the bottom of the evaporator.
The air flow in such a heat exchanger is controlled either by natural convection or by the installation of high-speed blower fans.
In ORV evaporators, seawater is typically used as a heat source for direct heating to vaporize liquefied gas. Sodium hypochlorite is injected at the entrance to the system to control algae growth. Specially treated seawater is pumped to the top of the heat exchanger and then passes through the outer surface of the heat exchanger tubes to provide highly efficient heat transfer.
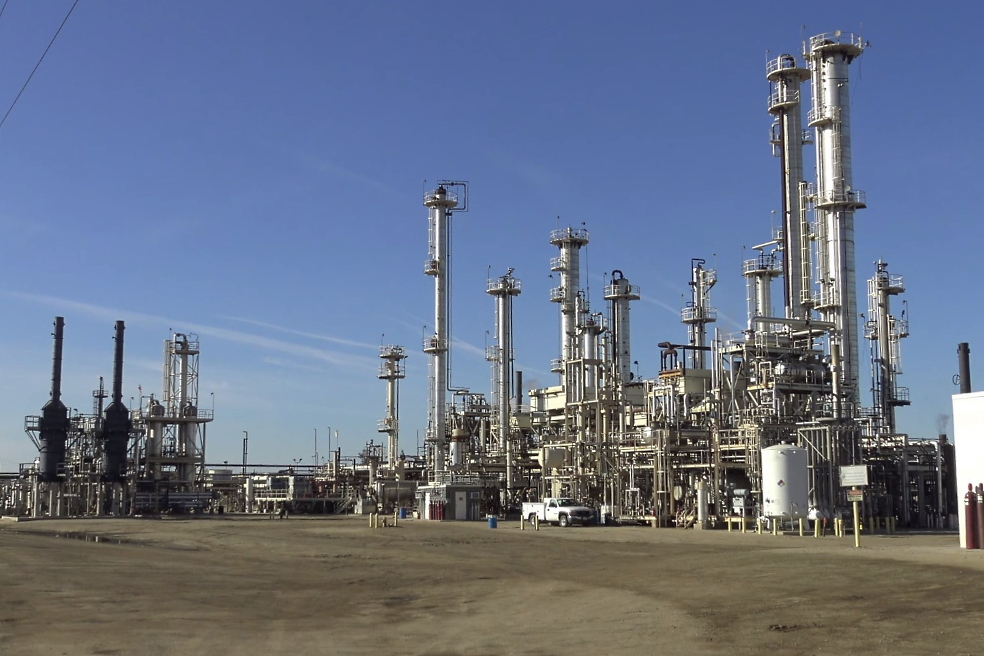
The cooled water then exits through the outlet, and the vaporized gas enters the chamber at the top.
This technology is effective if the water temperature is higher than 5 ° C.
Therefore, it is advisable to build regasification terminals of this type only in warm waters of non-freezing ports.
The choice of technology and specific equipment for the construction of LNG regasification terminals, despite significant progress in this area, remains a complex technical issue for engineering teams.
Construction of LNG terminals under the EPC contract: our services
Sedona Investments contributes to the development of LNG infrastructure by facilitating the financing and organization of the construction of liquefied natural gas terminals under the EPC contract.The geography of our services covers Latin America, Europe, USA, Canada, South Asia, China, North Africa and other regions of the world.
In most cases, we recommend to our clients the EPC model for the construction of LNG terminals as a simple, transparent and safe way to implement large capital-intensive projects with a large number of parties involved.
What are the advantages and limitations of this solution?
Most of the large oil and gas facilities were built by general contractors on EPC terms (Engineering, Procurement and Construction). These are specialized companies that are professionally engaged in engineering design, construction, procurement and installation of equipment. EPC contractors can often help arrange bridge financing or support the client in obtaining a loan on favorable terms.
The construction model using the services of an EPC contractor is the best choice for investors.
Such companies, thanks to many years of experience and developed contractual relations with leading manufacturers and suppliers, can receive favorable conditions for the purchase of equipment and the provision of technically complex services.
On the one hand, the construction of an LNG terminal under an EPC contract is more expensive (usually by 10-20%) compared to the traditional approach. On the other hand, this model looks much safer and more convenient for customers.
The traditional method, popular in real estate construction, is to find and enter into contracts with numerous contractors, manufacturers, suppliers, transport companies, institutes and so on. The problem is that small companies face high contractual risks here, requiring professional organization and project management.
Despite the perceived savings, the latter method of building LNG regasification terminals often leads to unforeseen downtime, longer work times and, finally, an increase in the cost of the project as a whole. This is especially the case for smaller companies that are taking on the risks of capital-intensive projects in the face of market uncertainty.
A serious problem for customers is the selection, purchase, import and installation of regasification equipment.
This requires sophisticated technical solutions, a deep understanding of the market for available technologies and additional investment costs.
The EPC contract minimizes the aforementioned project risks, as well as helps to reduce the project implementation time, which serves as an important competitive advantage in the rapidly changing global liquefied natural gas market.
Considering the construction of LNG terminals as an integral investment process from the project to the first gas intake, the whole process is often limited to 2-3 years. This deadline is realistic for most stakeholders, although it does not allow for slow decision-making.
Do you want to know more about the construction of liquefied natural gas infrastructure?
Looking for long term financing for LNG project in the EU or abroad?
Contact SI team to find out more.