Financing, engineering and construction of gas turbine power plants (GTPP)
Sedona Investments offers:
• Investment financing from £5 - 500 million or more
• Minimizing the contribution of the project promoter
• Investment loan term up to 10 years
• Credit guarantees
The EIA believes that fossil fuel-based thermal power plants will remain an important component of a reliable electricity supply until at least 2050.
With the rise of renewables, they will continue to stabilize the power system 24/7 regardless of wind speed or solar radiation.
Gas turbine power plants are capable of reaching full capacity in a few minutes, so they are especially suited to compensate for short-term peak loads. These flexible power plants will play an important role on the path to sustainable energy in the future.
These facilities are helping to close the gap that arises between electricity demand and the fluctuating renewable energy generation.
The investment costs for gas turbine power plants are relatively low compared to many other types of power plants, at around £ 1 million per megawatt of installed capacity.
The disadvantage of this type of power plant is its rather low efficiency (about 40%). If the waste heat generated during the combustion of fuel is additionally used to generate electricity, the efficiency of the system increases to 60-65%.
These facilities are known as combined cycle gas turbine (CCGT) plants.
The international company SI offers a full range of services related to the construction of gas turbine power plants, including the following:
• Project financing.
• Conducting a pre-investment assessment.
• Engineering design of a gas turbine power plant.
• Purchase of equipment from the world's leading manufacturers.
• Civil engineering and professional equipment installation.
• Launch and operation of facilities.
• Customer personnel training.
• Modernization and expansion.
• Maintenance and repair.
Contact SI consultants to learn more about our services.
Gas turbine power plants: basics
The beginning of the era of gas turbines dates back to the 18th century, and the first patents for gas turbines were issued at the end of the 19th century.However, the solutions proposed by Franz Stolze and Charles Curtis were useless for a long time, since the amount of energy required to operate the compressor exceeded the energy at the outlet of the turbine.
The construction of gas turbine power plants was impossible until the second half of the 20th century, as it was associated with exceeding the technical and temperature limits of materials and components used at that time in the production of turbines. In the following years, turbine development was mainly concentrated in aviation and missile weapons.
The 1950s were a period of rapid development of turbines and gas turbine engines.
World renowned manufacturers such as Westinghouse or General Electric have created engineering teams that have stepped up efforts to create new, more efficient devices.
The principle of operation of gas turbine power plants is simple. The intake air is compressed in the combustion chamber of the gas turbine and mixed with fuel (mostly natural gas). This mixture ignites and burns with the formation of gas with temperatures up to 1300-1500 degrees.
Modern, highly efficient turbines convert a significant portion of this thermal energy into kinetic energy of the rotating shaft. A multi-megawatt alternator connected to the turbine generates electricity.
A gas turbine power plant consists of several components:
• Gas turbine.
• Alternator and its infrastructure.
• Piping and duct systems.
• Air purification systems.
• Automatic control system.
• Electrical substation.
• Service platforms, etc.
It was not until the early 1960s that the use of gas turbines in the electric power industry gained new momentum.
This happened largely due to the advanced standardization of components. In the struggle for a market dominated by steam turbines, comprehensive packages of compressors, turbines and controls were proposed to create fully integrated power generation systems.
Thanks to standardization, such systems were mass-produced, and small individual changes were made almost immediately. This limited the workload for the designers and reduced the total cost of the components.
In addition, advances in new materials and cooling technologies have enabled manufacturers to increase gas temperature, resulting in improved overall system efficiency.
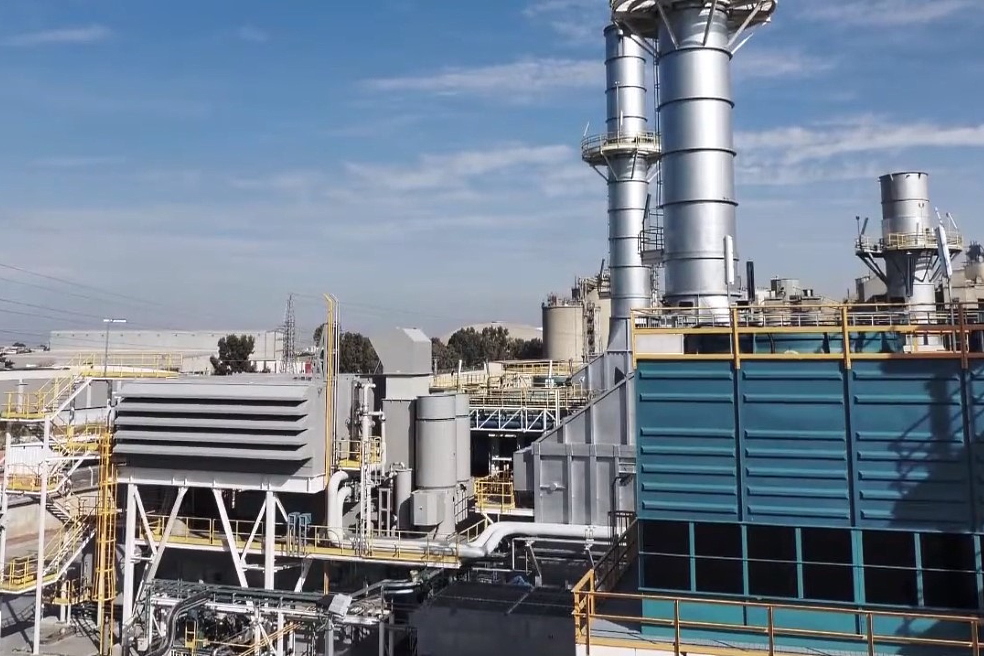
Benefits of gas turbines for the energy sector
The increased interest in the construction of gas turbine power plants has arisen due to the growing instability of energy systems.Experts say impressive power outages around the world have played a big role. The explosive growth of renewable energy sources has required the introduction of technologies that are able to cover the increasing load during peak hours.
These requirements are well met by modern thermal power plants based on gas turbines, which led to an increase in the number of these facilities in power systems in the 1970s. This area is successfully developing today.
Table: A quick comparison of gas and steam turbines for power generation.
Parameter | Gas turbines | Steam turbines |
Work cycle | Brayton cycle | Rankine cycle |
Power-to-weight ratio | High | Low |
Required space | Low | High |
Flexibility of operation | High | Low |
Water dependence | Low | High |
Efficiency | High | Low |
Construction time | Low | High |
The main feature of gas turbines is their high efficiency and quick start-up.
High operational efficiency is also the most important factor in the widespread use of these units in the energy sector. An additional argument in favor of gas turbines is the relatively low level of pollutant emissions into the environment.
Using natural gas as a fuel, a modern gas turbine reaches full power in just 5 minutes with a quick start. A reliable and flexible system allows companies to quickly restore power supply in emergency situations, guaranteeing the energy security of large enterprises and entire cities.
Equipment supply: gas turbine selection
When organizing the procurement of equipment for the construction of gas turbine power plants, it is important to agree on the required technical characteristics of each component of the turbine.For this, our engineering team conducts multi-stage consultations with customers.
The main structural elements of a gas turbine include an air intake, a compressor, a combustion chamber and the working section itself.
When choosing equipment for the construction of a gas turbine power plant, our experienced specialists determine the balance of the technical characteristics of each of these elements so that the system meets the requirements of the customer company and current standards as much as possible.
Inlet
The gas turbine air intake system supplies clean air to the turbine under the most suitable pressure and temperature conditions.Inlet filters of various types are installed, which are responsible for removing particulate matter. In this part, special systems are also installed that regulate the temperature and contribute to the maximum supply of prepared air to the turbine.
Air compressor
The function of the compressor is to increase the pressure of the filtered air for more efficient combustion of the fuel before it enters the combustion chamber.Air and fuel are mixed in a ratio that depends on the type of turbine, but usually ranges from 10: 1 to 40: 1. The air compression process takes place in several stages and consumes a significant part of the energy produced by the gas turbine.
The air intake is controlled by changing the angle of inclination of the compressor blades. The larger the angle, the more air flows into the compressor and therefore into the combustion chamber. This equipment is used to improve the part-load performance of a gas turbine.
Some of the air from the compressor is used to cool the blades and the combustion chamber, so that about 50% of the total air is used for this purpose.
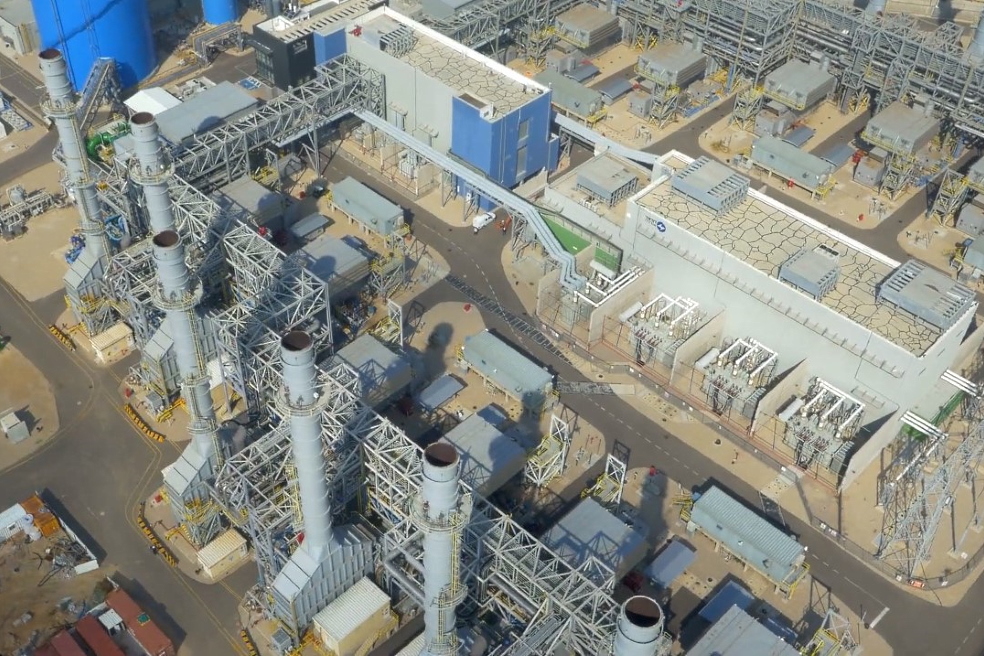
The combustion chamber
In the combustion chamber, the combustion of the gas-air mixture takes place at the optimum pressure.This process requires the supply of fuel at a suitable pressure, which is in the range of 15 to 50 bar. To achieve optimal temperatures and extend component life, modern turbines use 300 to 400% of the theoretical combustion air volume.
This ensures effective control of the flame temperature and, on the other hand, helps to cool the hottest parts of the chamber.
Some of the air leaving the compressor is directed towards the walls of the combustion chamber in order to keep its temperature low enough. Another part of the air circulates between the blades of the gas turbine, exiting through the holes in the edges. The parameters of the combustion chamber largely determine the characteristics of a particular turbine.
Turbine
The main part of the turbine (shaft with multiple rows of blades) efficiently converts the energy contained in the hot gas into mechanical energy from the shaft rotation.A significant part of the energy generated is consumed directly by the compressor.
The gases that enter the turbine at a temperature of 1300-1500ºC and a pressure of 10 to 30 bar exit the nozzle at 450-600ºC. This high temperature means that the energy contained in the gases can be used to improve the performance of a gas turbine power plant, including generating steam in a waste heat recovery unit (WHRU).
Then this steam is injected into a separate steam turbine, increasing the efficiency of the system to 60-65% (the efficiency of the gas turbine is 35-40%).
The current trend in the development of thermal power engineering is the gradual modernization of old TPPs using a combined steam-gas cycle. This technical solution provides a significant increase in power generation and improved economic efficiency of facilities.
Construction of gas turbine power plants under the EPC contract
As technology advances, it becomes clear that the construction of gas turbine power plants requires the involvement of numerous engineering teams and the active implementation of innovative technologies at all stages of the project.With project costs amounting to hundreds of thousands of euros for each megawatt of installed capacity, gas turbine power plants are traditionally considered to be very expensive energy facilities. Bank loans and project financing, technical and legal advice, selection of suppliers and contractors - the responsibility for the smooth implementation of such projects is enormous.
The international company SI is ready to become your reliable assistant in the implementation of large energy projects according to the EPC model.
An EPC (engineering, procurement, construction) contract is sometimes referred to as a turnkey construction.
This is a special form of contractual relationship based on the signing of a single contract with the general contractor, who is fully responsible for the implementation of the project.
SI and its partners offer financing and engineering services, professional selection and procurement of equipment, as well as turnkey TPP construction.
Engineering includes the following works:
• Planning.
• Conducting field research.
• Approval and obtaining permits.
• Drawing up a construction estimate.
• Preparation of technical documentation.
At this stage, the customer is presented with options for the project of a gas turbine power plant based on the research results.
It is important to find the best solution in order to get the maximum return with the lowest possible investment.
The stage of purchasing and supplying equipment includes:
• Drafting requirements.
• Organization and holding of tenders.
• Negotiations with manufacturers and suppliers.
• Acceptance and quality control of equipment.
• Delivery of equipment to the site.
The customer can be sure that turbines, transformers, generators, electronic equipment and all materials required to start construction will be ordered, delivered and paid strictly on time.
The construction stage is the most time consuming:
• Coordination of the construction schedule.
• Transportation of materials to the construction site.
• Construction works: metal structures, buildings, panels, cables, fences.
• Consultations with customers / investors and reports from the construction site.
• Contracts with subcontractors for certain types of work.
• Completion and commissioning of the facility.
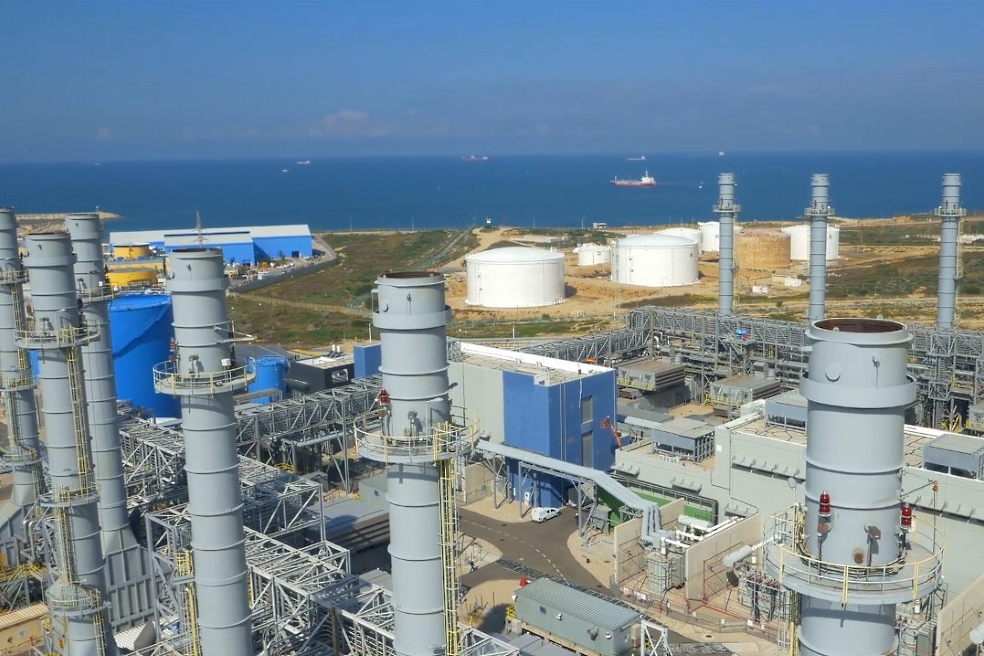
The EPC formula has many benefits for the customer.
First of all, it is convenience and confidence that the entire process of construction of a gas turbine power plant must be carried out in accordance with current legislation and technical requirements.
SI with partners are ready to take full responsibility for the implementation of your ambitious project from the drawing stage to start-up and operation.
Directions of modernization of gas turbine power plants
Aviation gas turbines have always required the smallest size and maximum reliability.In the power industry, size and weight are no longer an issue.
A more important factor was the reduction in turbine manufacturing costs.
Thus, now we can talk about two different technologies with their own ways of development.
The first gas turbines had separate compressor and turbine systems. These were ineffective and technologically complex solutions. Currently the most widely used solution is to place the compressor and turbine on the same axis.
This simplifies the design, increases the reliability and efficiency of the entire system.
One of the directions of modernization of the gas turbine power plant is to increase the fuel combustion temperature, which became possible due to the use of resistant materials and the latest design solutions. Combustion chambers are now designed to minimize NOx emissions.
Manufacturers currently offer different types of combustion chambers.
For example, these can be independent devices located outside the structure of the turbine itself. Some of the latest technical solutions are multi-section chambers arranged in a ring around the gas turbine.
Over the past decades, progress in this area has been limited by the thermal properties of the materials from which the first stage of the turbine is made.
Significant progress has also been made in this area. Back in the 1960s, the usual inlet gas temperature was 900 ° C, but already in the 1970s this value increased to 1100 ° C. The currently used solutions allow reaching 1500-1600 ° C.
Recently, the work of gas turbine engineers has mainly focused on the development of new materials that can meet the increasing demands for higher gas temperatures. Research is carried out using unusual materials such as ceramics, which are becoming an alternative to the metals currently in use. Many additional operating procedures are also being investigated to improve efficiency and gas turbines.
The working medium at the turbine inlet is carefully filtered to exclude any impurities.
These measures protect the turbine blades from damage, increase operational reliability and extend its service life. Water vapor is also injected into the compressor along with the fuel. This operation dramatically increases the productivity and efficiency of systems. Cooling systems for turbine blades are actively used in modern high-temperature turbines.
An important role is played by computerization and automation of gas turbine power plants, which makes it possible to optimize the load of power units taking into account the current needs of the power grid.
Installation of state-of-the-art hardware and software provides a significant reduction in NOx emissions by 60-80% while increasing operational flexibility without costly measures.
If you are interested in expanding or funding a gas turbine power plant, you can contact our team at any time and receive detailed advice on the key aspects of your project.